Overview
- Structural Steel Plate Processor
- Hypertherm Plasma Cutting
- Triple Tool Punch Press
- SignoScript Carbide Scribing
- Roller Feed Measurement
- Side Unloading System
- Nesting Software
- Siemens Advanced Control
Process
Punch Press
Utilize 100% of Shop Plate Production
Capable of plasma cutting, punching and scribing, the FPB-1800 is the chosen solution for steel fabricators and service centers. 80% of any shop's plate production is on 1" (25 mm) thick material or less, making this machine a perfect supplement to your heavy plate processing.
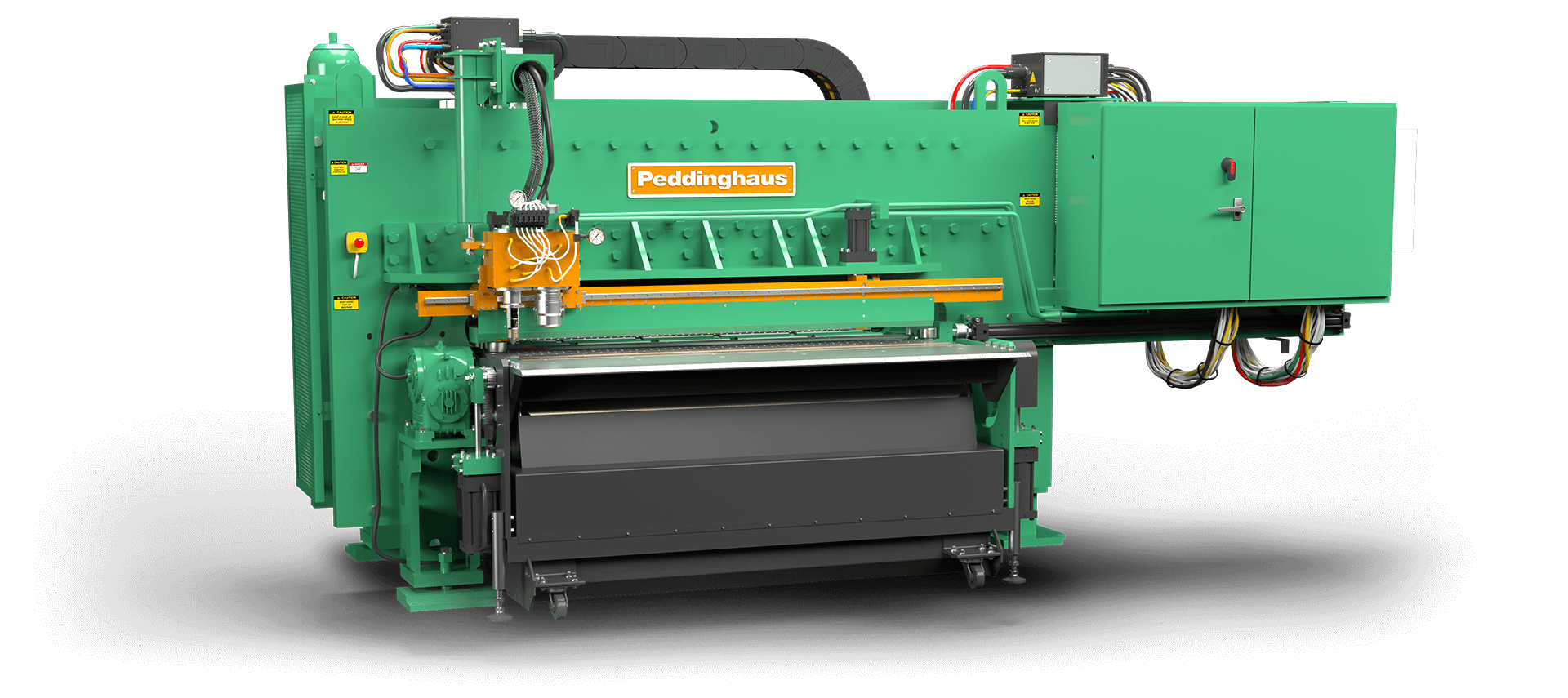
Ditch the Burn Table, Save Money
The CNC plate processing design by Peddinghaus drives material to the operating area of the machine as opposed to bringing the operating area of the machine to the material, like traditional burntable systems. The FPB-1800 provides constant material output to downstream processes.
Plasma Cut 1” Thick Plate
When it comes to plate production, the FPB-1800 provides maximum durability with innovative cutting techniques. The FPB-1800 performs flawlessly for processing parts up to 1-1/4" (32 mm) thick. On average, 80% of shop plate production is 1" (25 mm) thick material and under.
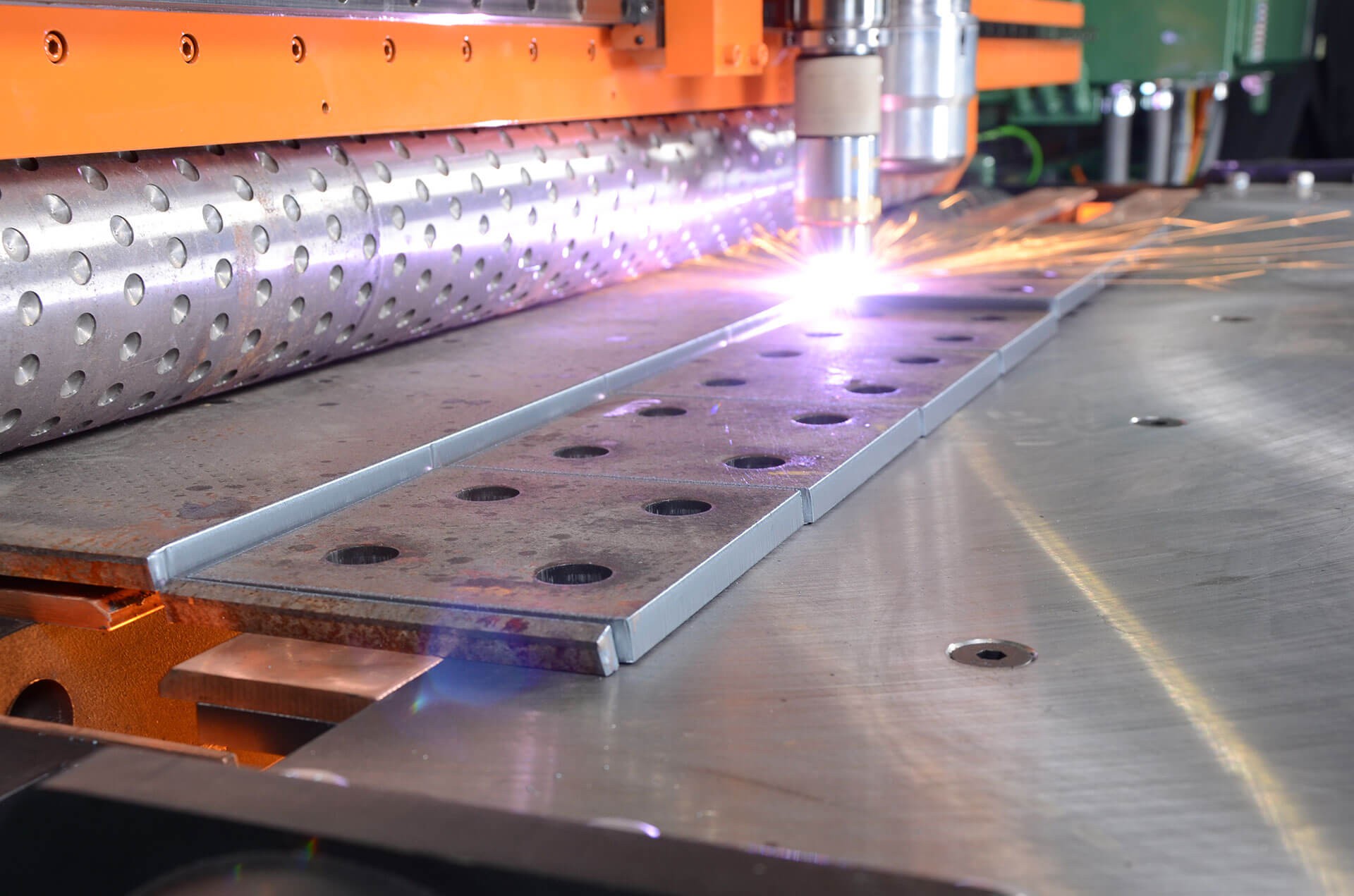
Efficiently Process with the Triple Tool Punch Press
The most cost-effective way to process holes in steel plate up to 1" (25 mm) thick is by using the FBP-1800 CNC plate punching machine. The proven 177 ton triple tool punch press of the FPB-1800 allows for maximum durability and efficiency. Capable of punching holes up to 1-3/4" (44 mm) in diameter, and maintaining up to three available punch stations, the FPB-1800 minimizes the need for timely tool changes.
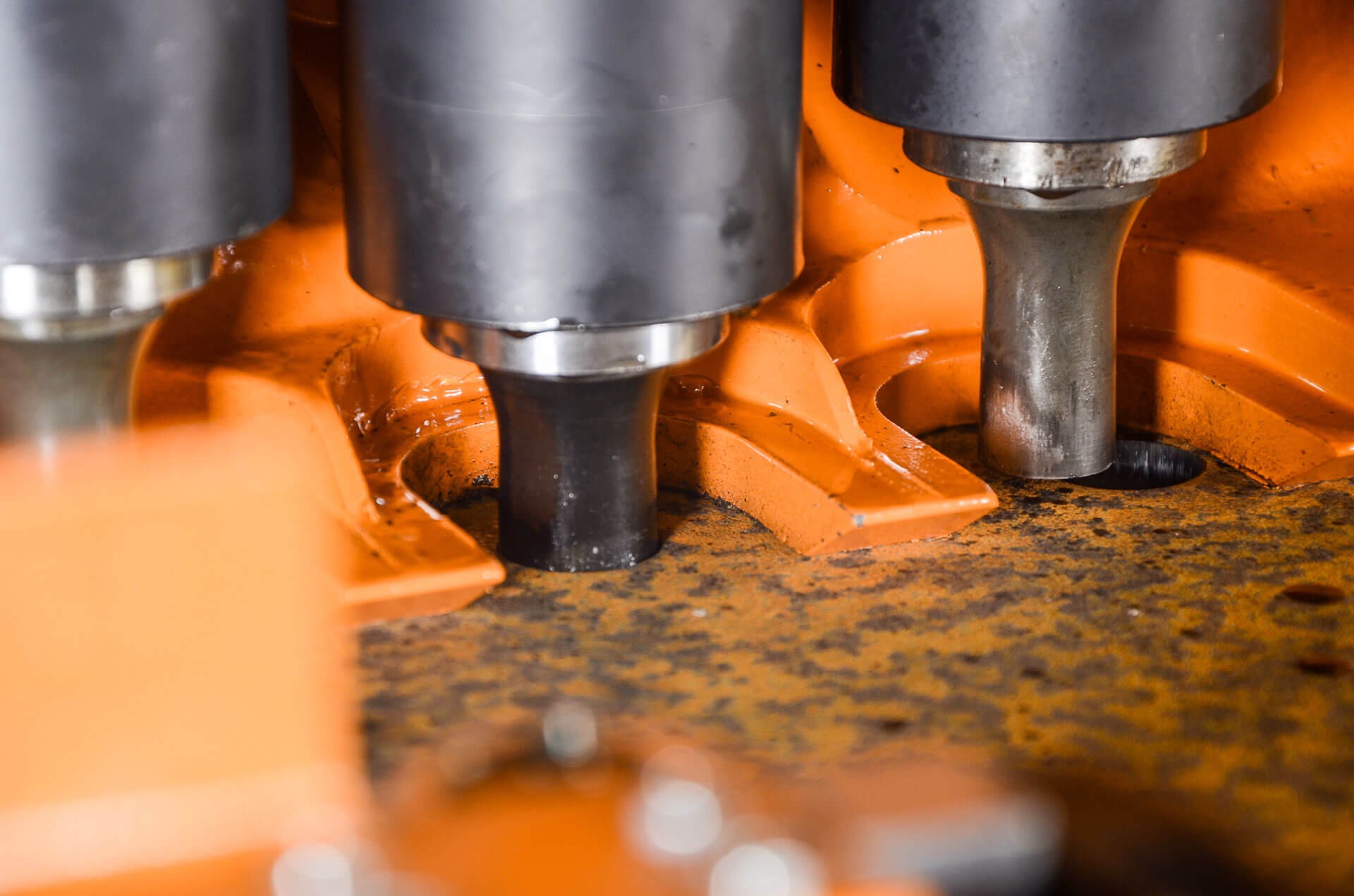
Punch for Pennies Per Hole
The punch press of the FPB-1800 maintains a unique "soft c-frame" design. This ensures that the punch, once aligned with the die, maintains crisp positioning for seamless and repeatable punch cycles, eliminating the risk of the punch colliding with the die and damaging tooling. This dramatically reduces consumable costs.
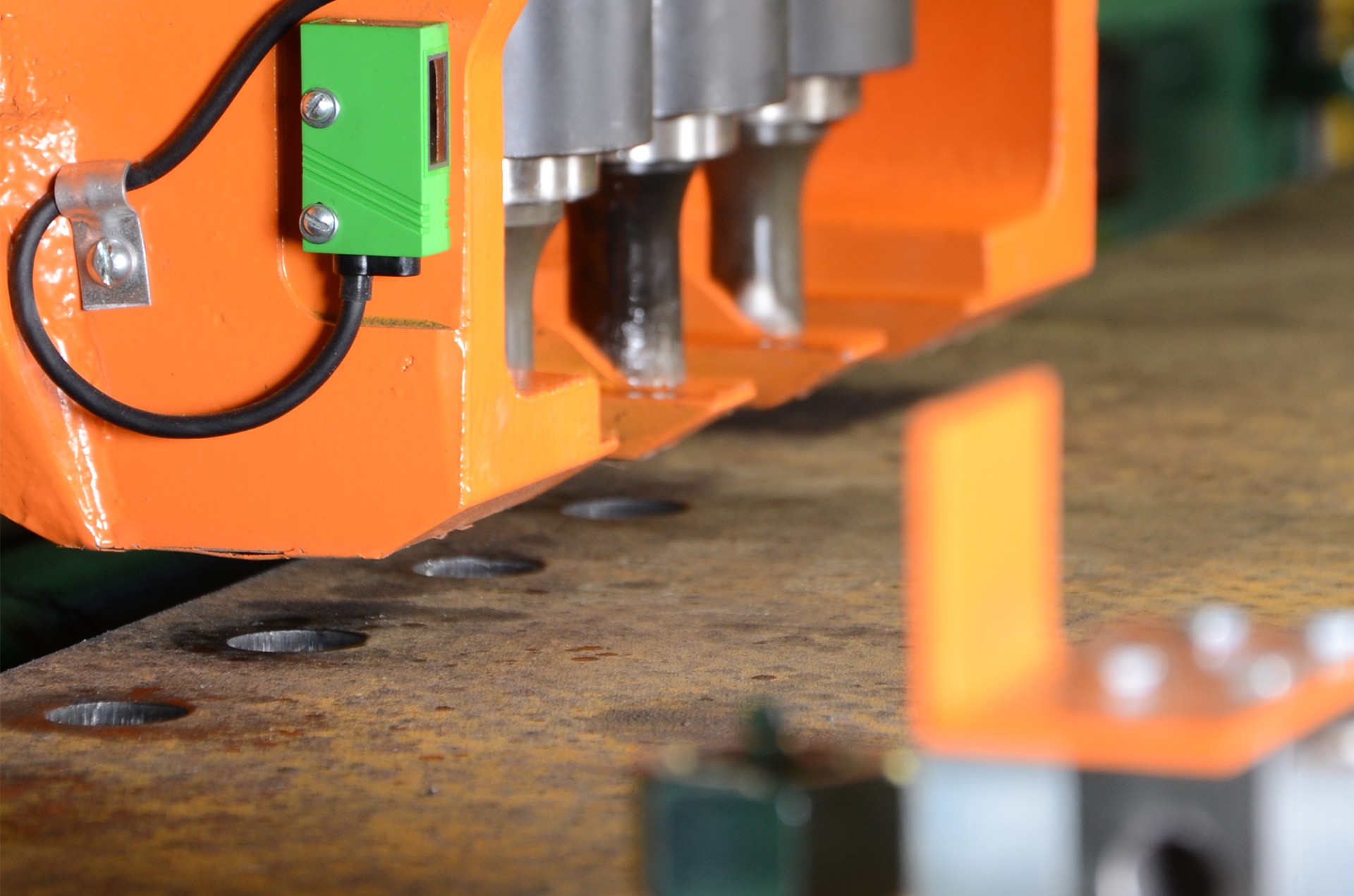
Speed And Versatility Benefits Downstream Production
This CNC plate processing design drives material to the operating area of the machine as opposed to bringing the operating area of the machine to material, like traditional burntable systems. The FPB-1800 provides constant material output for welders and fitters, allowing them to focus on assembling the end-product.
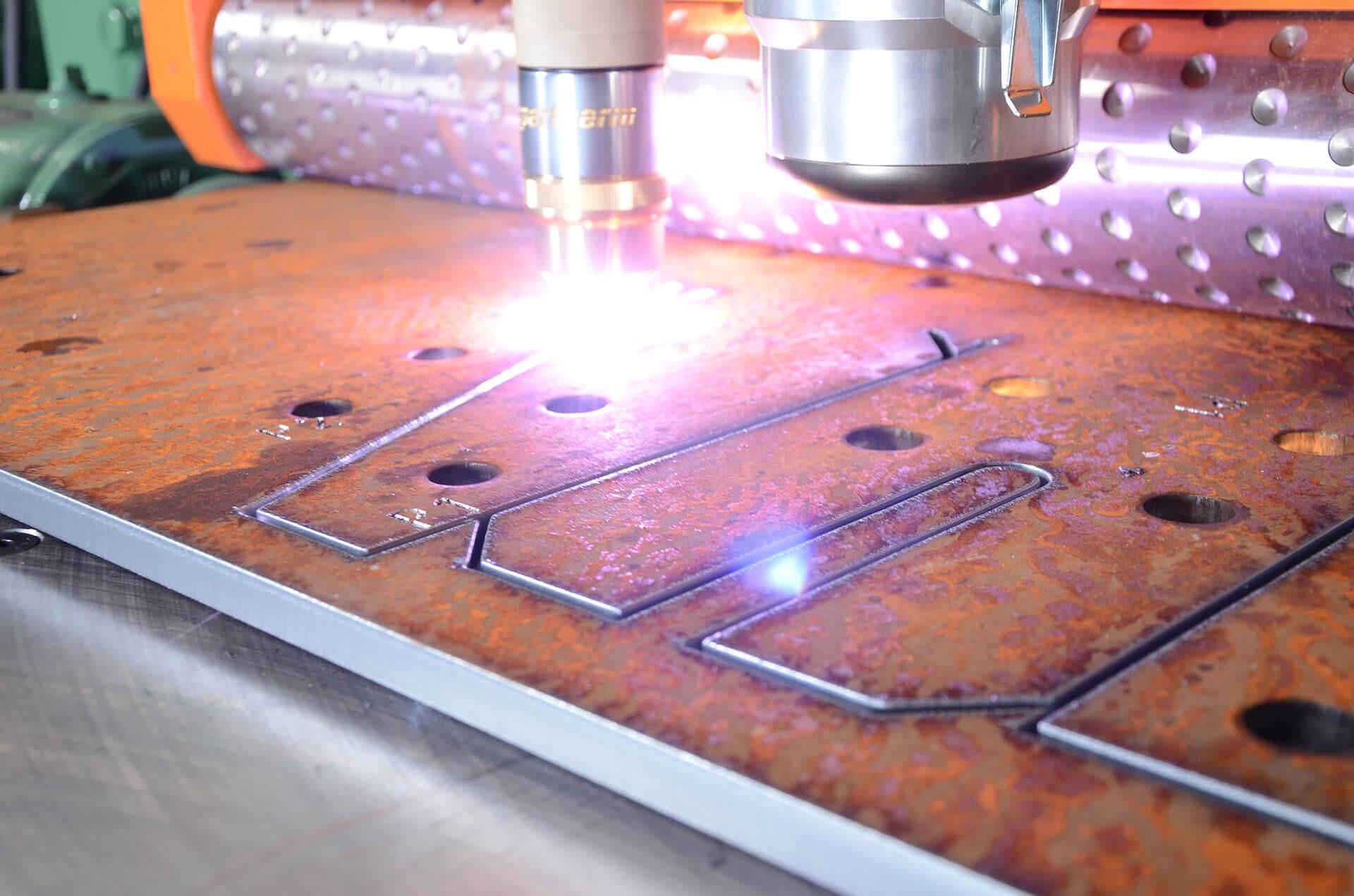
Nonstop Throughput with Roller Feed Measurement
Equipped with the Peddinghaus Roller Feed measurement system, the FPB-1800 maintains contact with the material at all times.
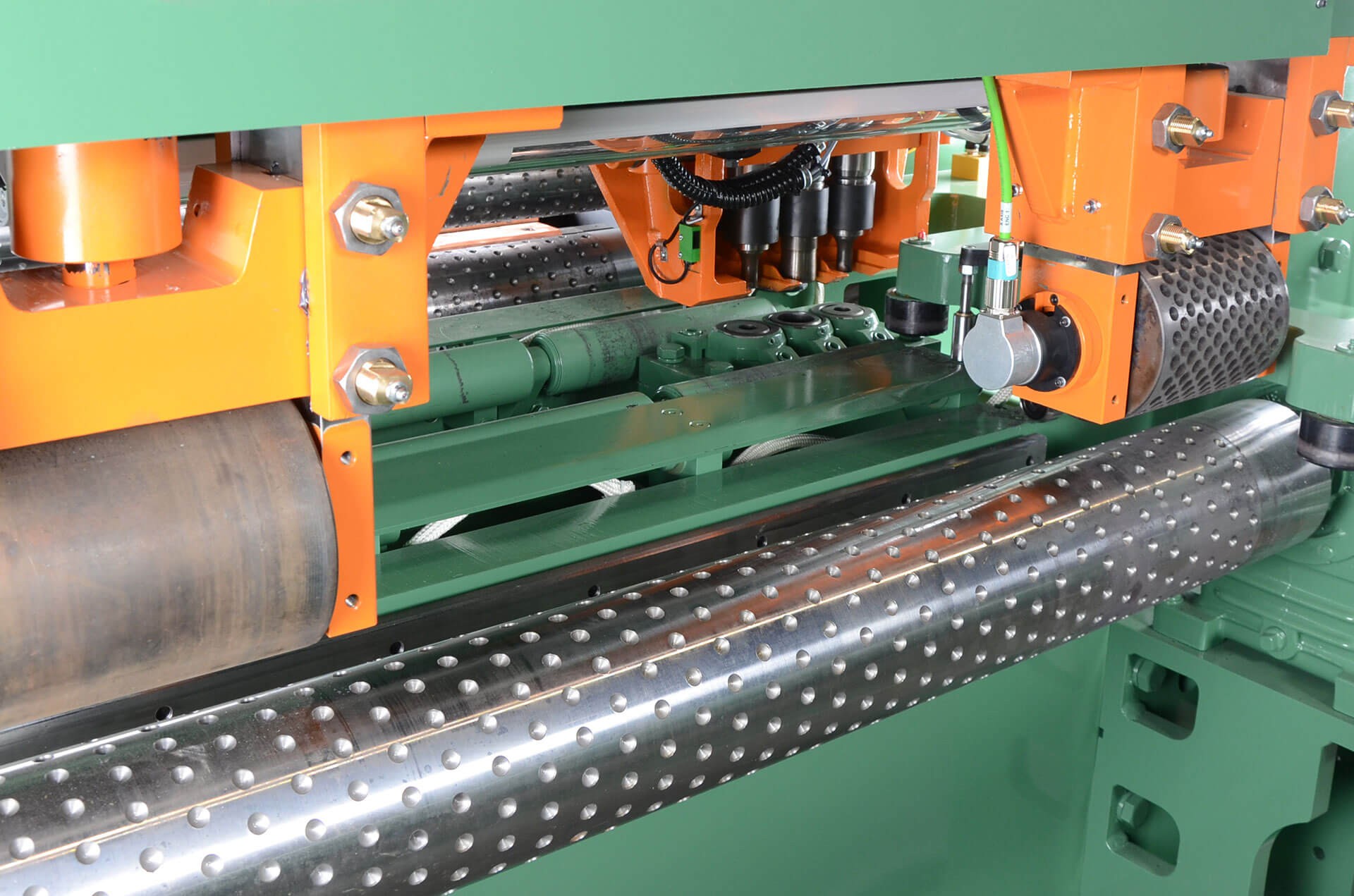
SignoScript Carbide Scribing
The SignoScript layout marking attachment eliminates human error in manual layout methods. Complete information is maintained throughout blasting, galvanizing and painting processes.
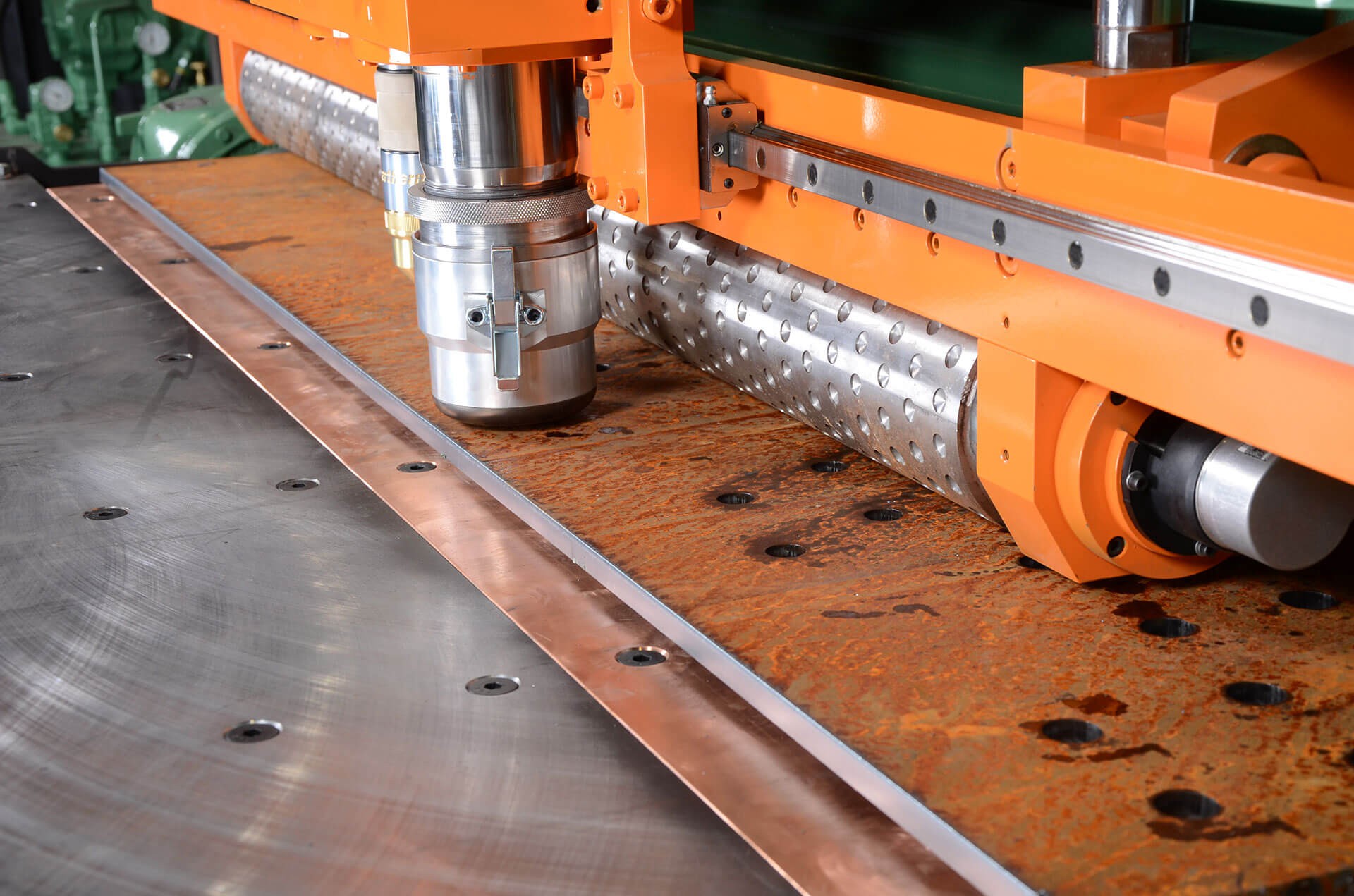
The Side Unloading System
The Side Unloader parts conveyor is designed to allow finished parts to drop directly onto a hardened steel conveyor, delivering them to an ergonomic unloading height at the operator station. The Side Unloader conveyor option transfers parts while the machine is in continuous operation.

SDS Plate Nesting Software
Peddinghaus plate machines proudly operate with today’s modern nesting software solution, SDS. SDS software allows fabricators to automatically batch nest existing files, edit on the fly or create parts at the control console. Peddinghaus machines are able to take full advantage of common cutline, chain cutting and edge start cutting techniques.
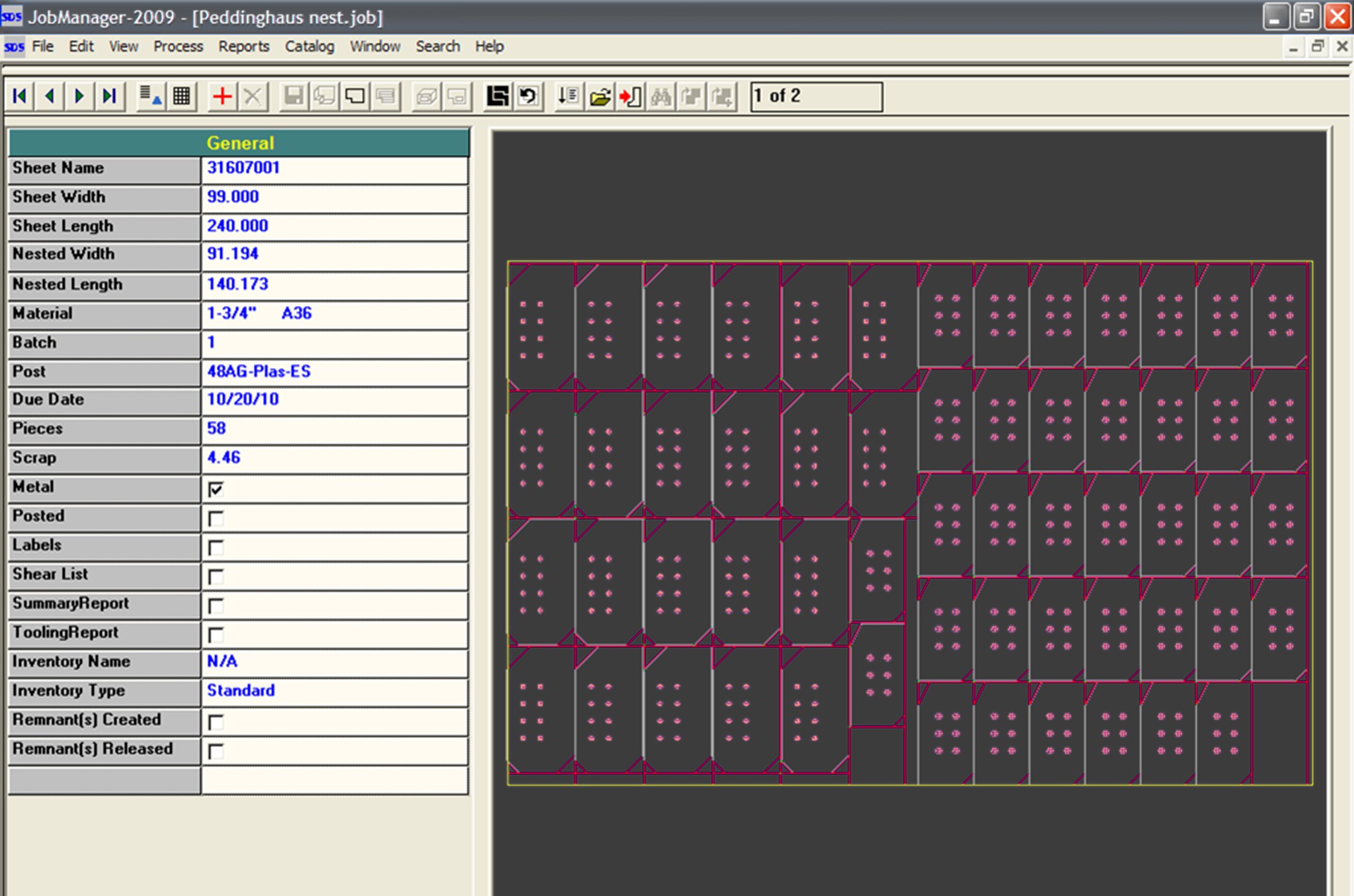
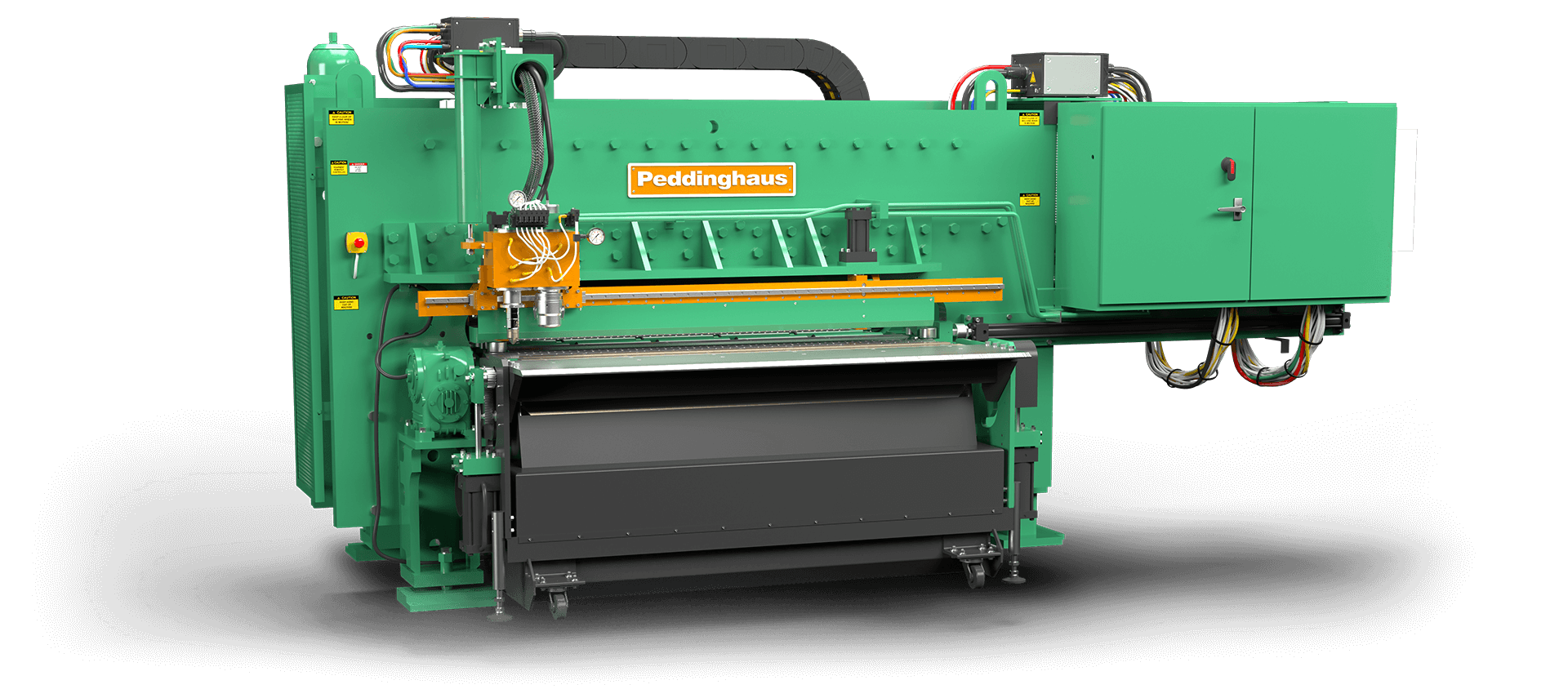
Utilize 100% of Shop Plate Production
Capable of plasma cutting, punching and scribing, the FPB-1800 is the chosen solution for steel fabricators and service centers. 80% of any shop's plate production is on 1" (25 mm) thick material or less, making this machine a perfect supplement to your heavy plate processing.
Ditch the Burn Table, Save Money
The CNC plate processing design by Peddinghaus drives material to the operating area of the machine as opposed to bringing the operating area of the machine to the material, like traditional burntable systems. The FPB-1800 provides constant material output to downstream processes.
Plasma Cut 1” Thick Plate
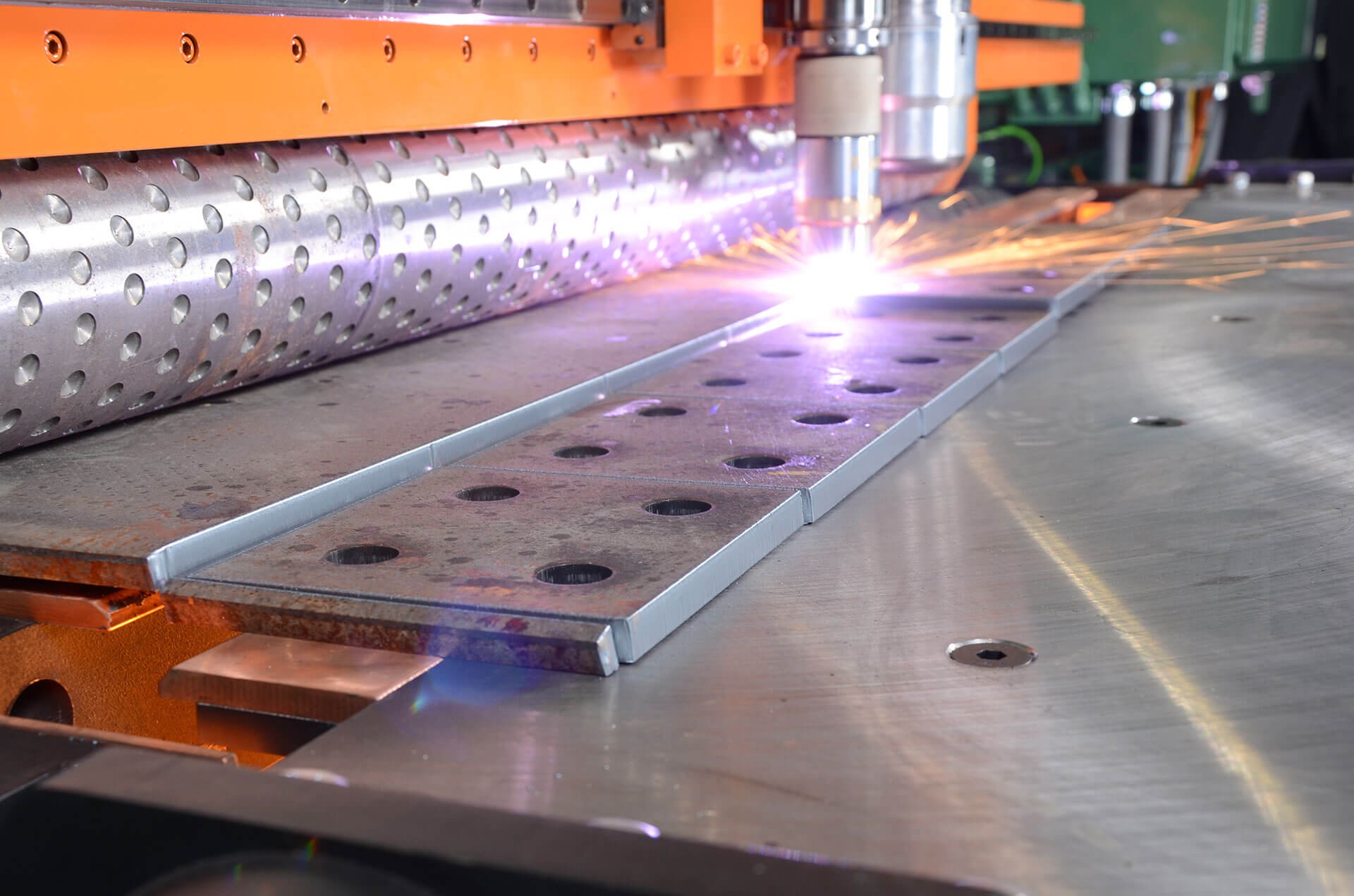
When it comes to plate production, the FPB-1800 provides maximum durability with innovative cutting techniques. The FPB-1800 performs flawlessly for processing parts up to 1-1/4" (32 mm) thick. On average, 80% of shop plate production is 1" (25 mm) thick material and under.
Efficiently Process with the Triple Tool Punch Press
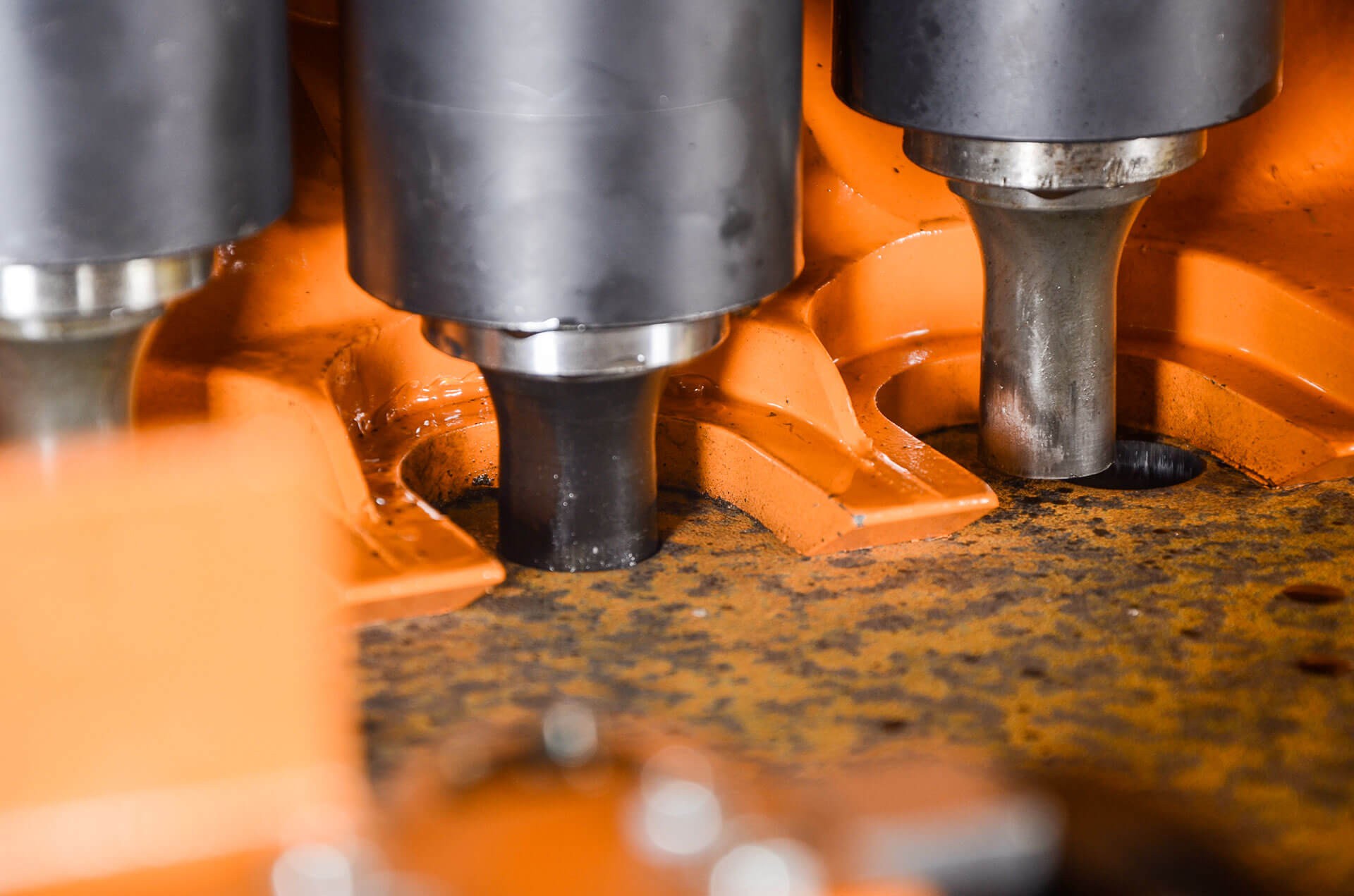
The most cost-effective way to process holes in steel plate up to 1" (25 mm) thick is by using the FBP-1800 CNC plate punching machine. The proven 177 ton triple tool punch press of the FPB-1800 allows for maximum durability and efficiency. Capable of punching holes up to 1-3/4" (44 mm) in diameter, and maintaining up to three available punch stations, the FPB-1800 minimizes the need for timely tool changes.
Punch for Pennies Per Hole
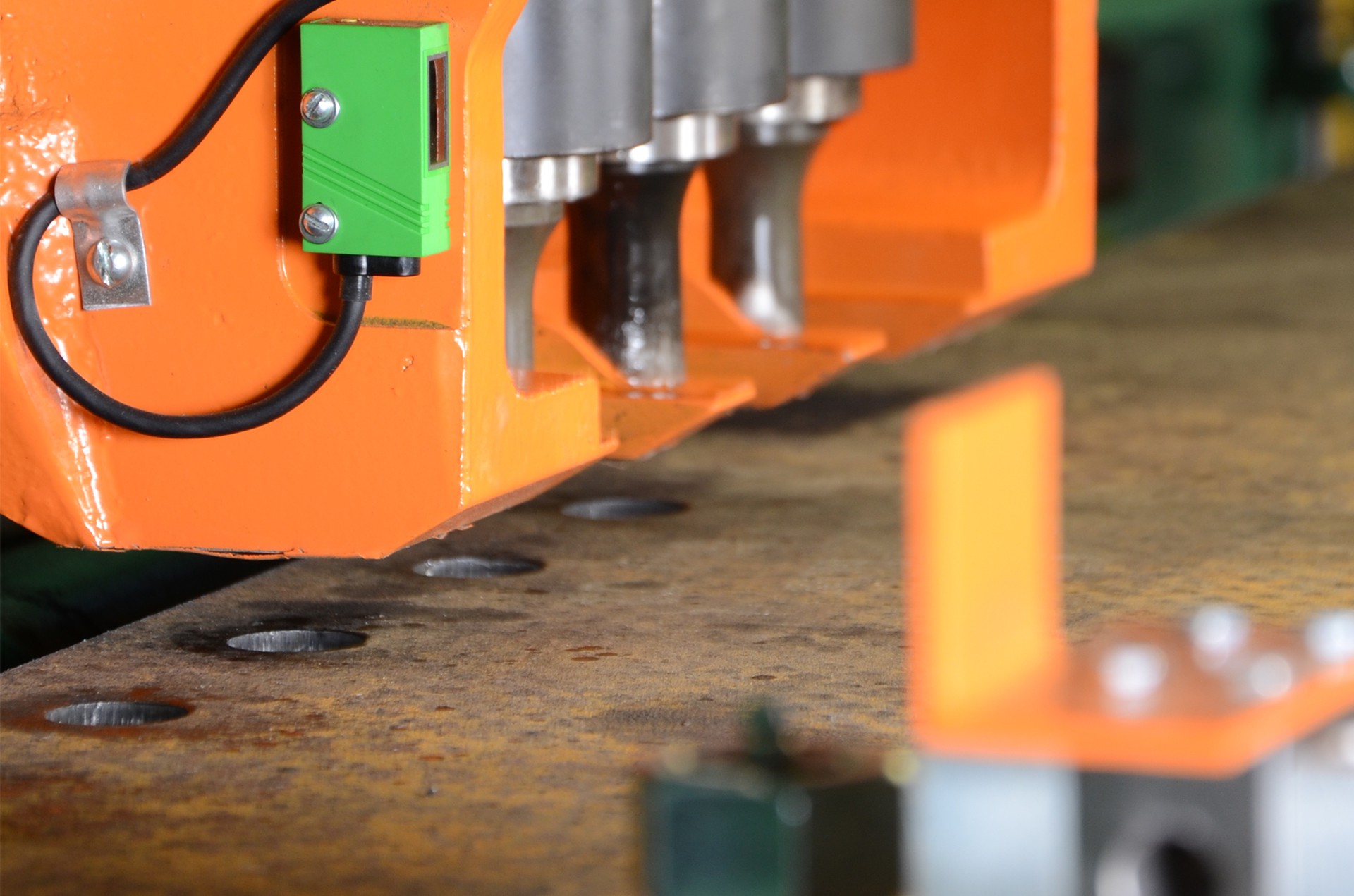
The punch press of the FPB-1800 maintains a unique "soft c-frame" design. This ensures that the punch, once aligned with the die, maintains crisp positioning for seamless and repeatable punch cycles, eliminating the risk of the punch colliding with the die and damaging tooling. This dramatically reduces consumable costs.
Speed And Versatility Benefits Downstream Production
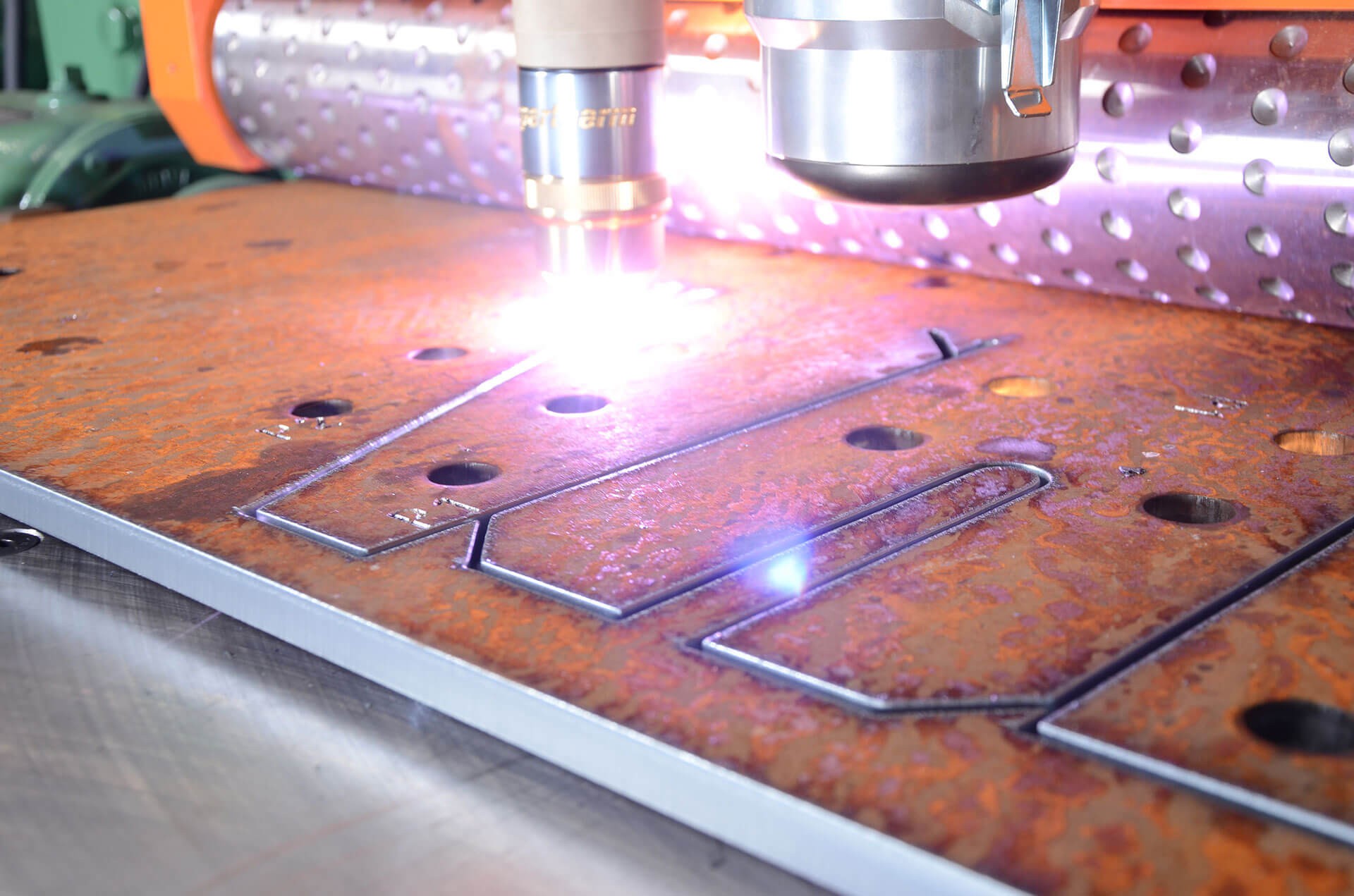
This CNC plate processing design drives material to the operating area of the machine as opposed to bringing the operating area of the machine to material, like traditional burntable systems. The FPB-1800 provides constant material output for welders and fitters, allowing them to focus on assembling the end-product.
Nonstop Throughput with Roller Feed Measurement
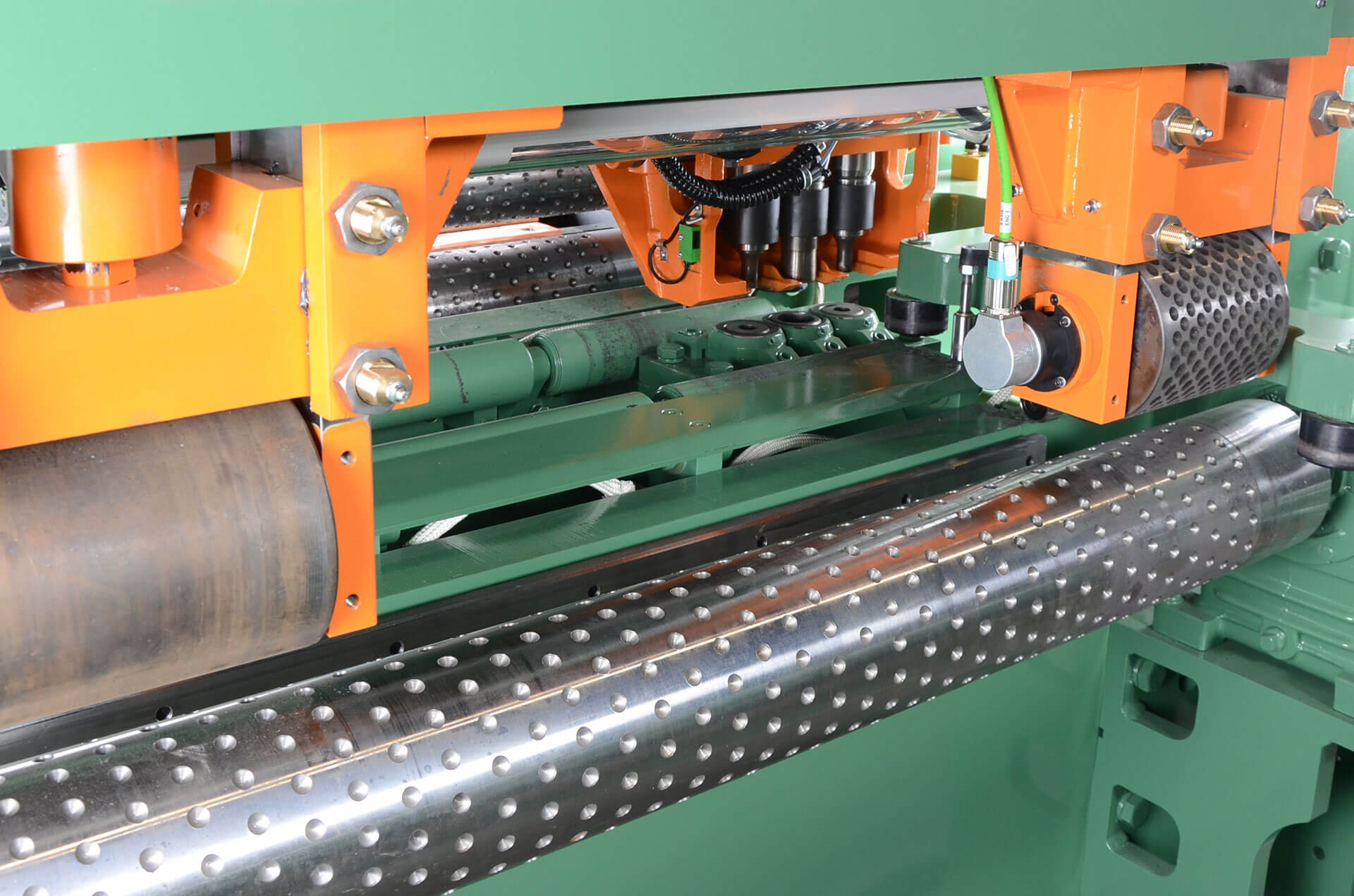
Equipped with the Peddinghaus Roller Feed measurement system, the FPB-1800 maintains contact with the material at all times.
SignoScript Carbide Scribing
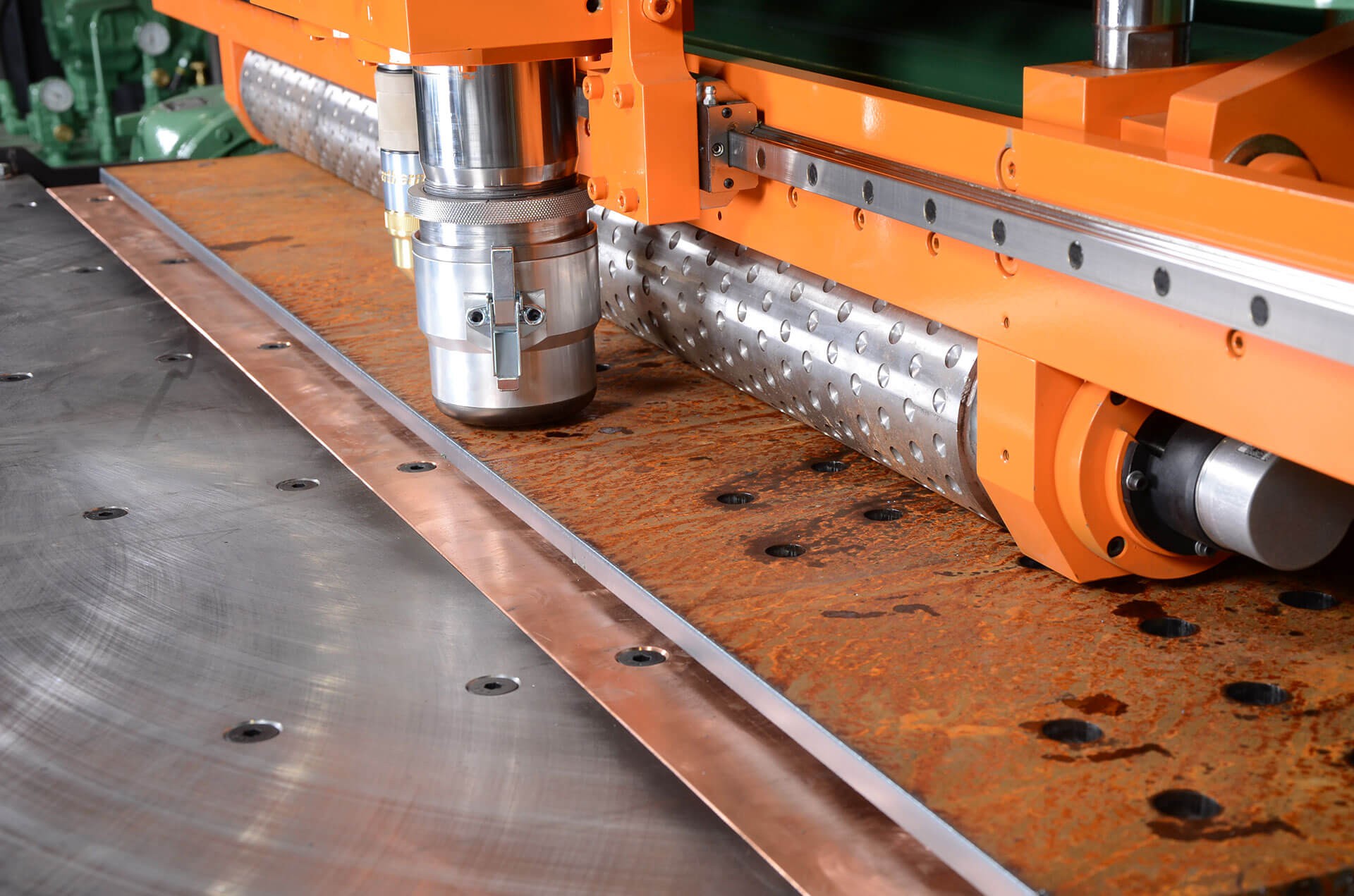
The SignoScript layout marking attachment eliminates human error in manual layout methods. Complete information is maintained throughout blasting, galvanizing and painting processes.
The Side Unloading System
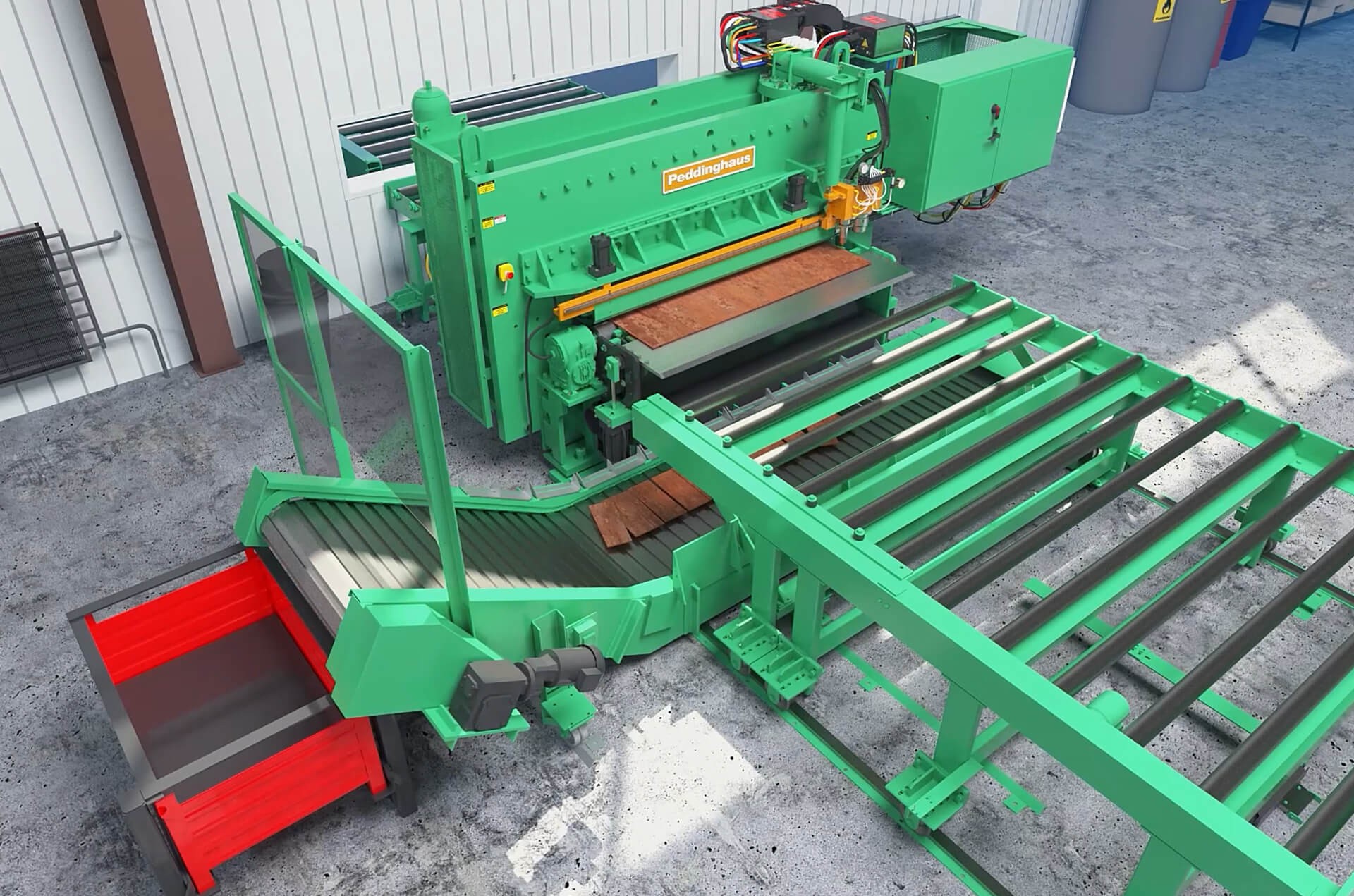
The Side Unloader parts conveyor is designed to allow finished parts to drop directly onto a hardened steel conveyor, delivering them to an ergonomic unloading height at the operator station. The Side Unloader conveyor option transfers parts while the machine is in continuous operation.