Overview
- Angle and Flat Line
- SignoScript Carbide Scribing
- SignoMat Part Stamping
- Roller Feed Measurement
- Minimum Quantity Lubrication
- Superior Clamping System
- Peddinghaus Control
- Raptor Software
- Punching
- Shearing
- Nibbling
- Material Handling
Shear
Punch
Process Higher Volumes of Angle
Detail components make up the smallest tonnage of any fabricators' workload, but consistently demand the highest amount of labor. Serving as the industry's benchmark for productivity and accuracy, the Anglemaster-663 caters to today's fabricators' need to automate punching, nibbling, shearing and marking for angle and flat bar.
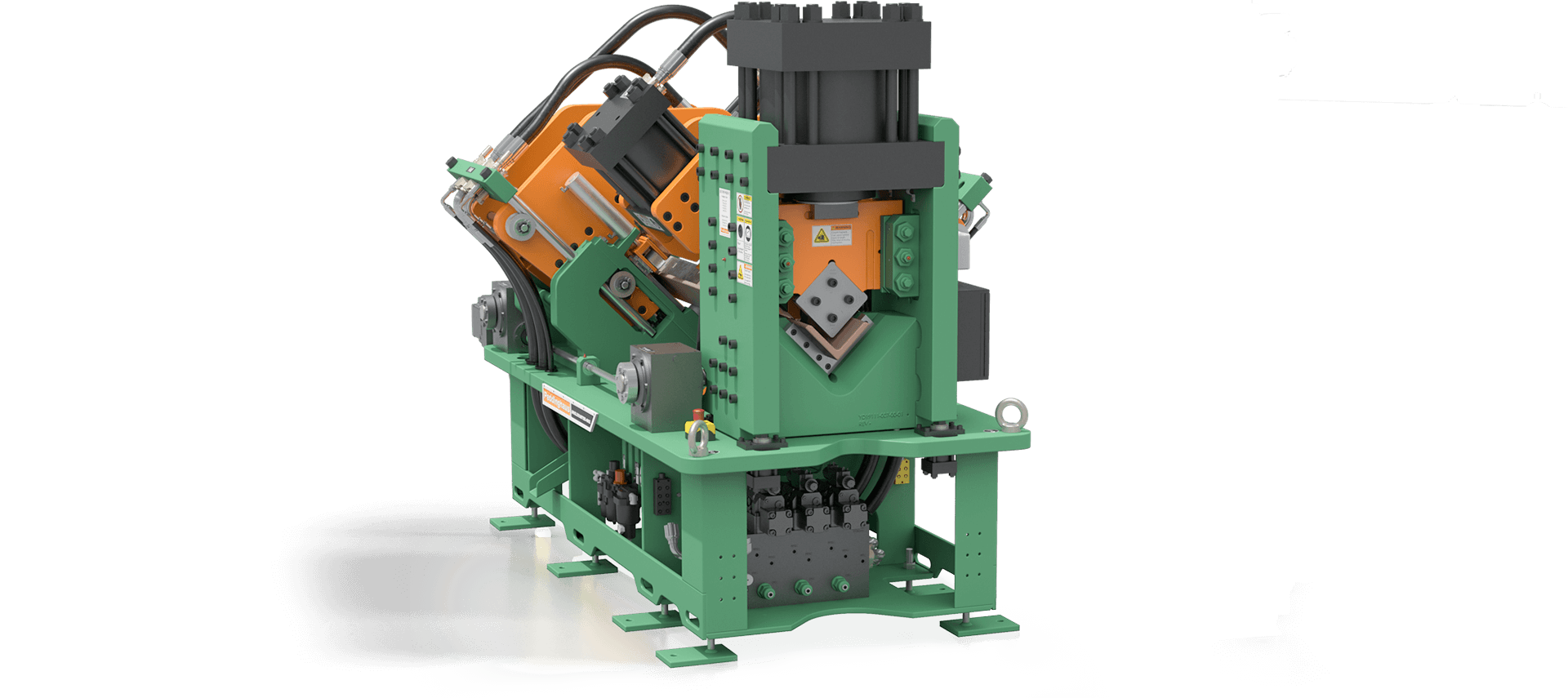
Accurate and Versatile Angle Processing
The Roller Feed drive and measurement system from Peddinghaus has been redesigned to improve accuracy even greater than before. By positioning two encoders on the machine, steel can pass through piece after piece with no stop in production. This innovative patented Roller Feed is designed to flex with the material in order to ensure a constant roll and an accurate measurement given deviations in material, maximizing contact with long parts.
6 Punches for Tooling Capacity
Three punch stations per hydraulic press allow the machine to apply up to three different hole shapes/sizes per leg. A new and improved punch tool design allows for quicker and easier tool changes. This angle line can accommodate shaped holes such as squares, rectangles, obrounds and slots, including a feature that allows nibbling of material for cutting large notches out of angle or flat bar.
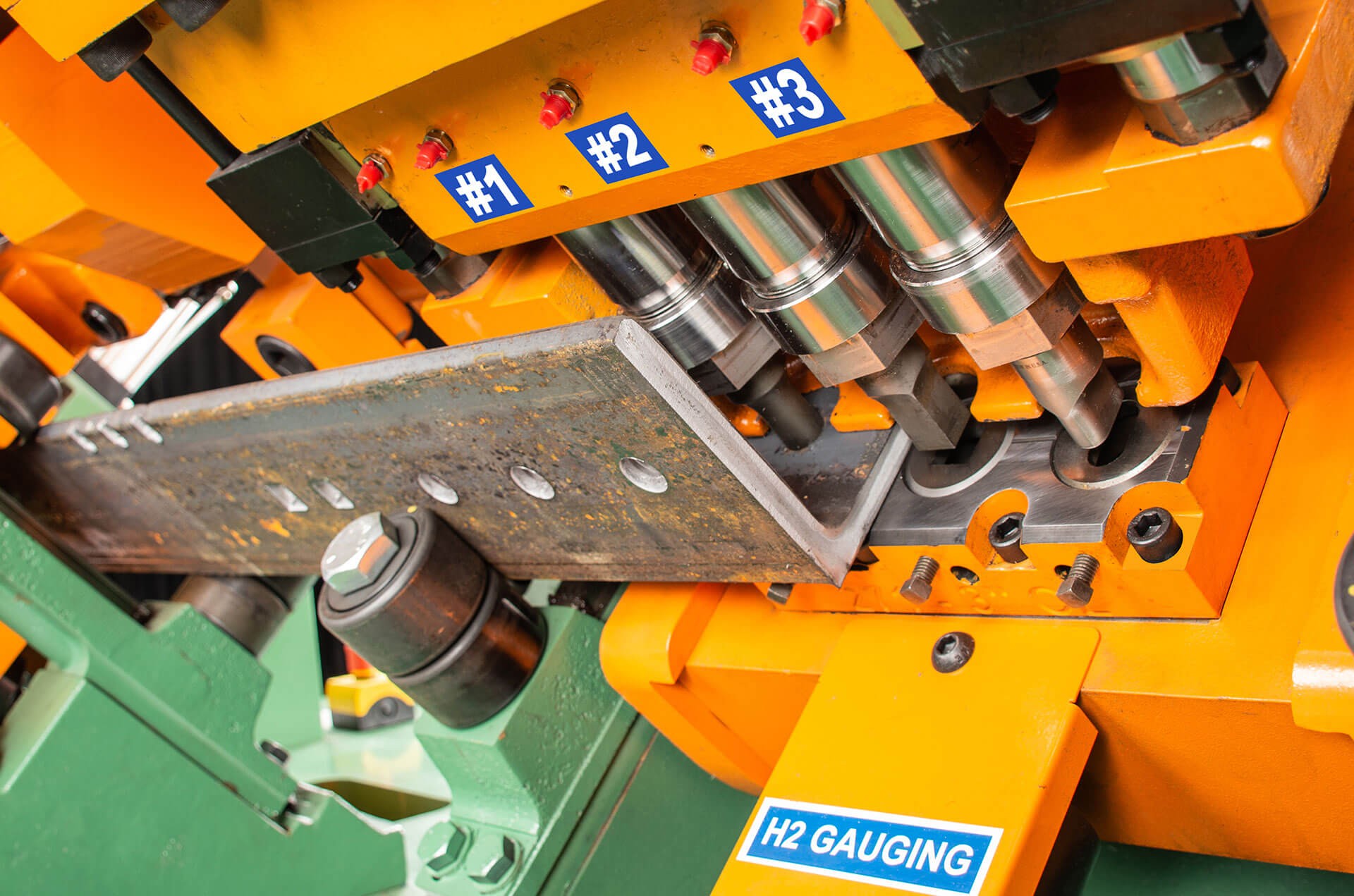
Powerful Shearing
The Anglemaster-663 uses a single cut 320 ton shear press for the cutting to length angle and flat stock. A single cut shear mechanism eliminates the slug created by double cut shear mechanisms.
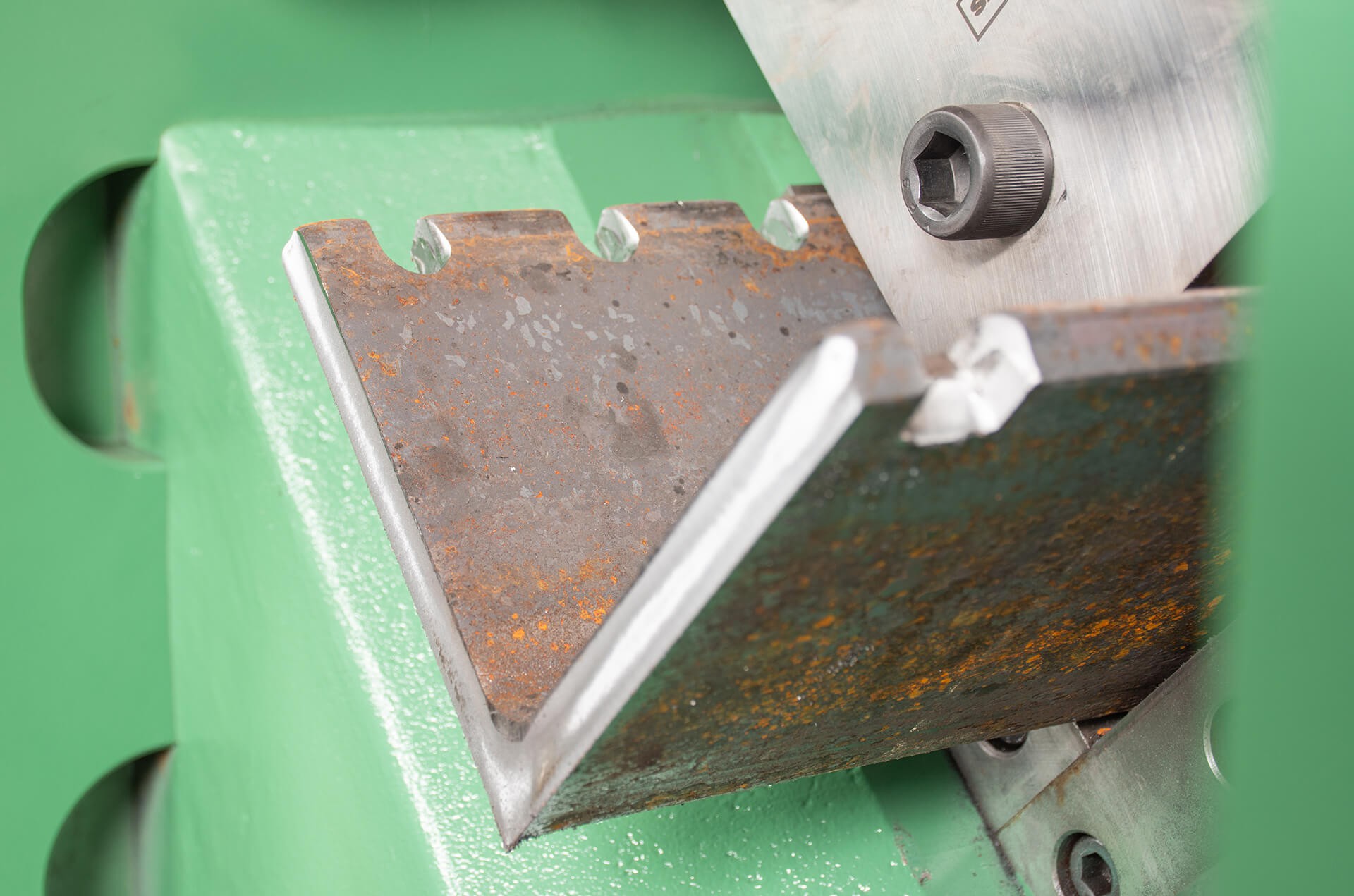
SignoScript Carbide Scribing
The SignoScript layout marking attachment eliminates human error in manual layout methods. Complete information is maintained throughout blasting, galvanizing and painting processes.

SignoMat Part Stamping
The SignoMat part stamping unit stamps at an unmatched 1 character per second with a depth of 1/32" (.8 mm) and a total height of 1/2" (12 mm). The unit holds up to 36 characters for complete part marking ability.
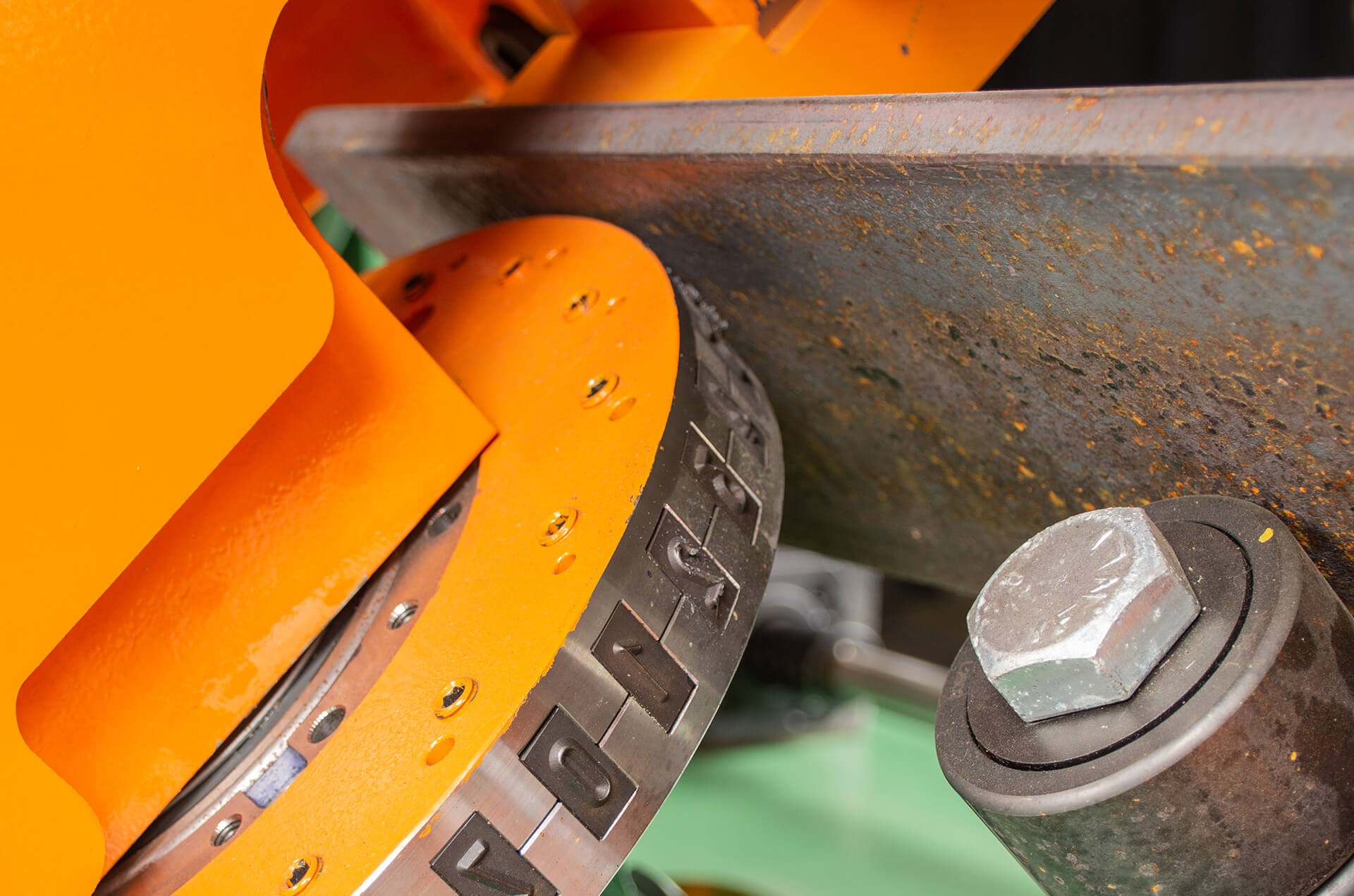
Nonstop Throughput with Roller Feed Technology
Equipped with the Peddinghaus Roller Feed measurement system, the Anglemaster-663 maximizes contact with the material at all times. This Roller Feed technology ensures a constant roll and an accurate measurement given deviations in material.
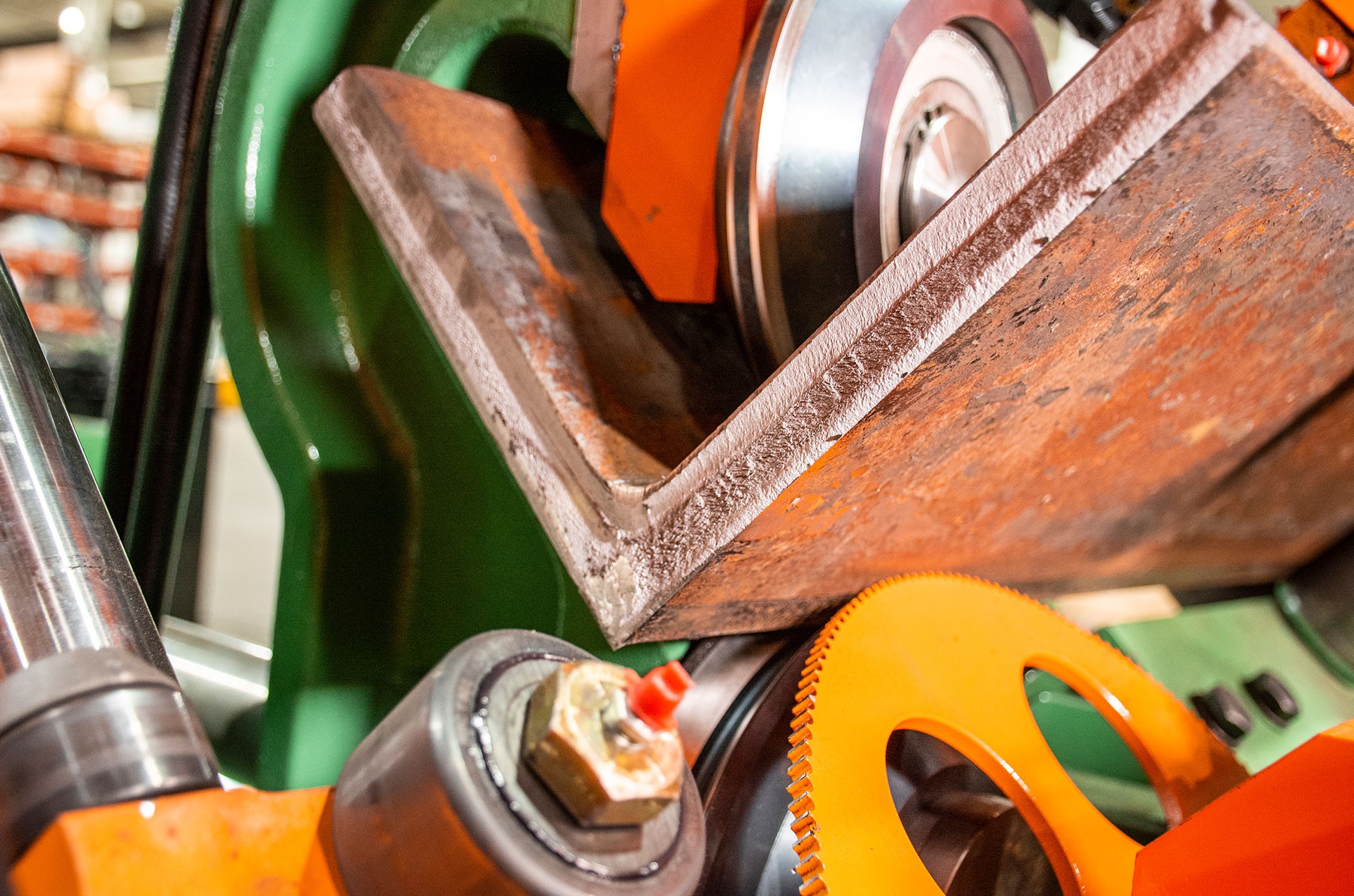
Lubrication System Prolongs Tool Life
The lubrication system on the Anglemaster-663 angle line extends to the shear, now allowing for longer shear life. Overall angle production and tool life is enhanced with the Minimum Quantity Lubrication (MQL) system.
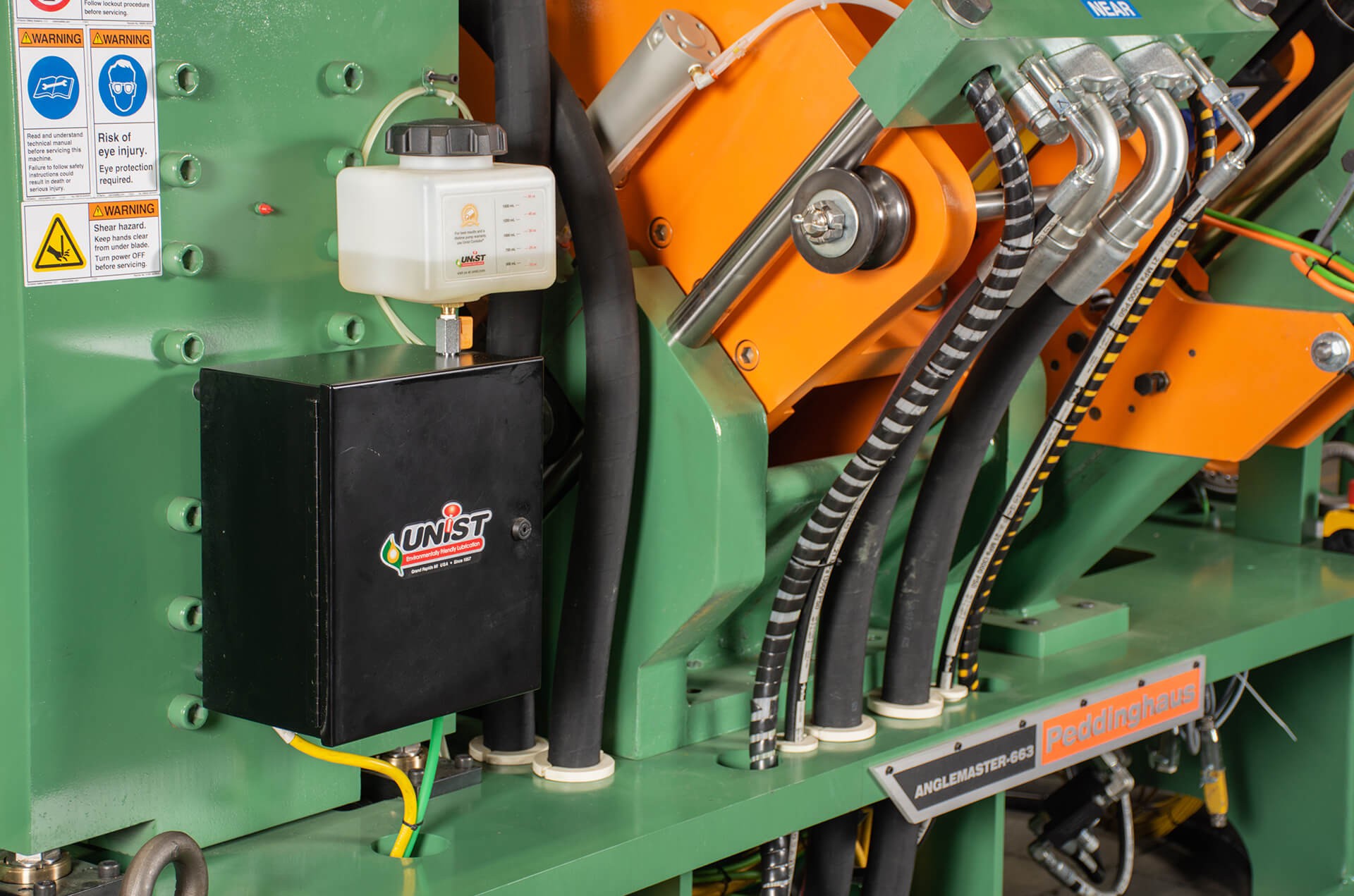
Infeed and Outfeed Material Handling
The infeed and outfeed material handling system, designed for continuous production, keeps the operator safe at all times. As drag chain conveyors move material to the infeed conveyors, power material advance initiates steel into the machine. Once sheared, drive rollers advance the finished parts to the unloading zone.
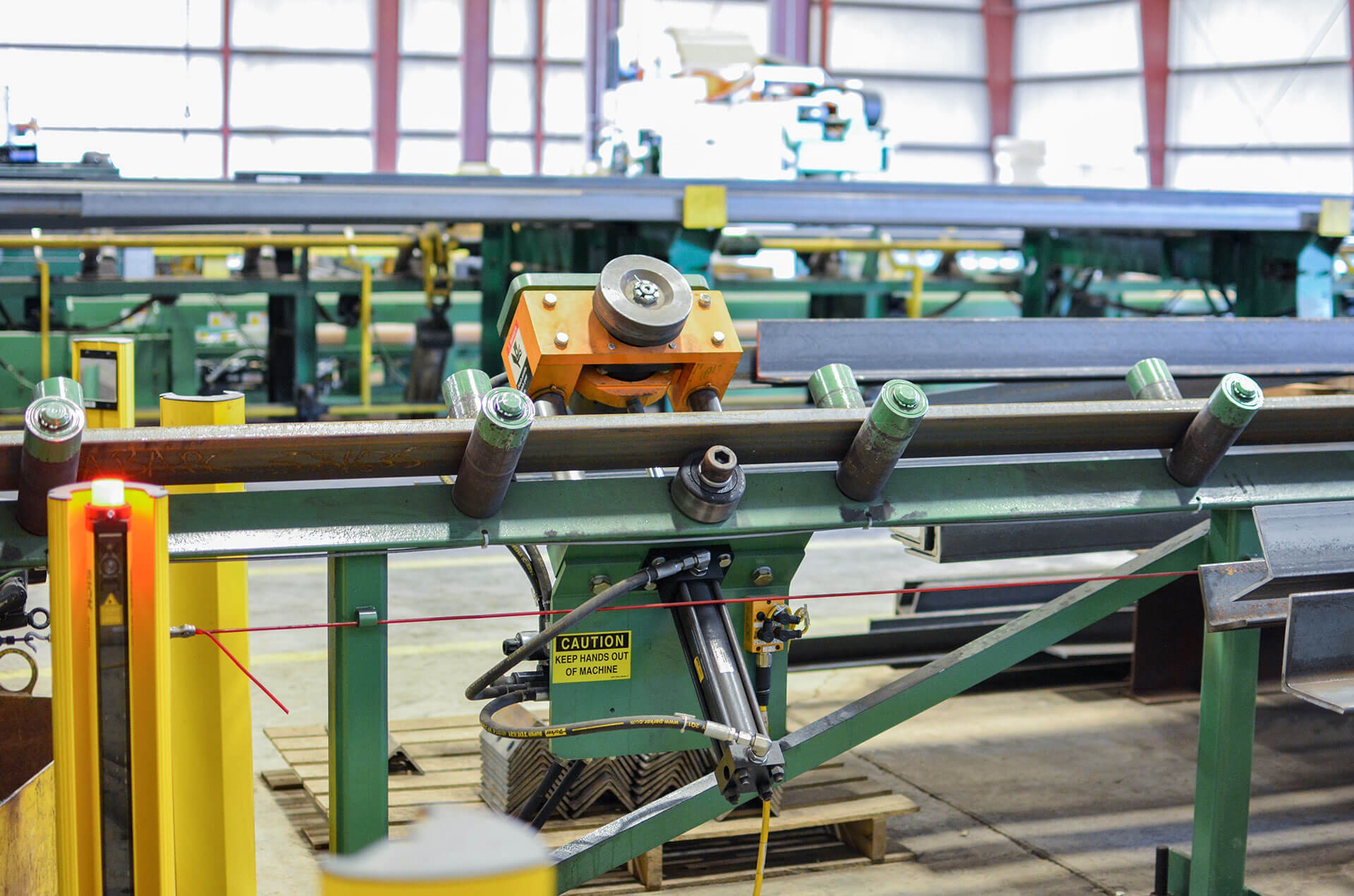
Raptor 3D CAD/CAM Software
Developed by Peddinghaus, Raptor 3D CAD/CAM Software takes CNC innovation further by enabling users to program faster and more accurately. Inspect, modify and export part information directly within the 3D platform. This coupled with Peddinghaus CNC technology means maximum capacity for fabricators.
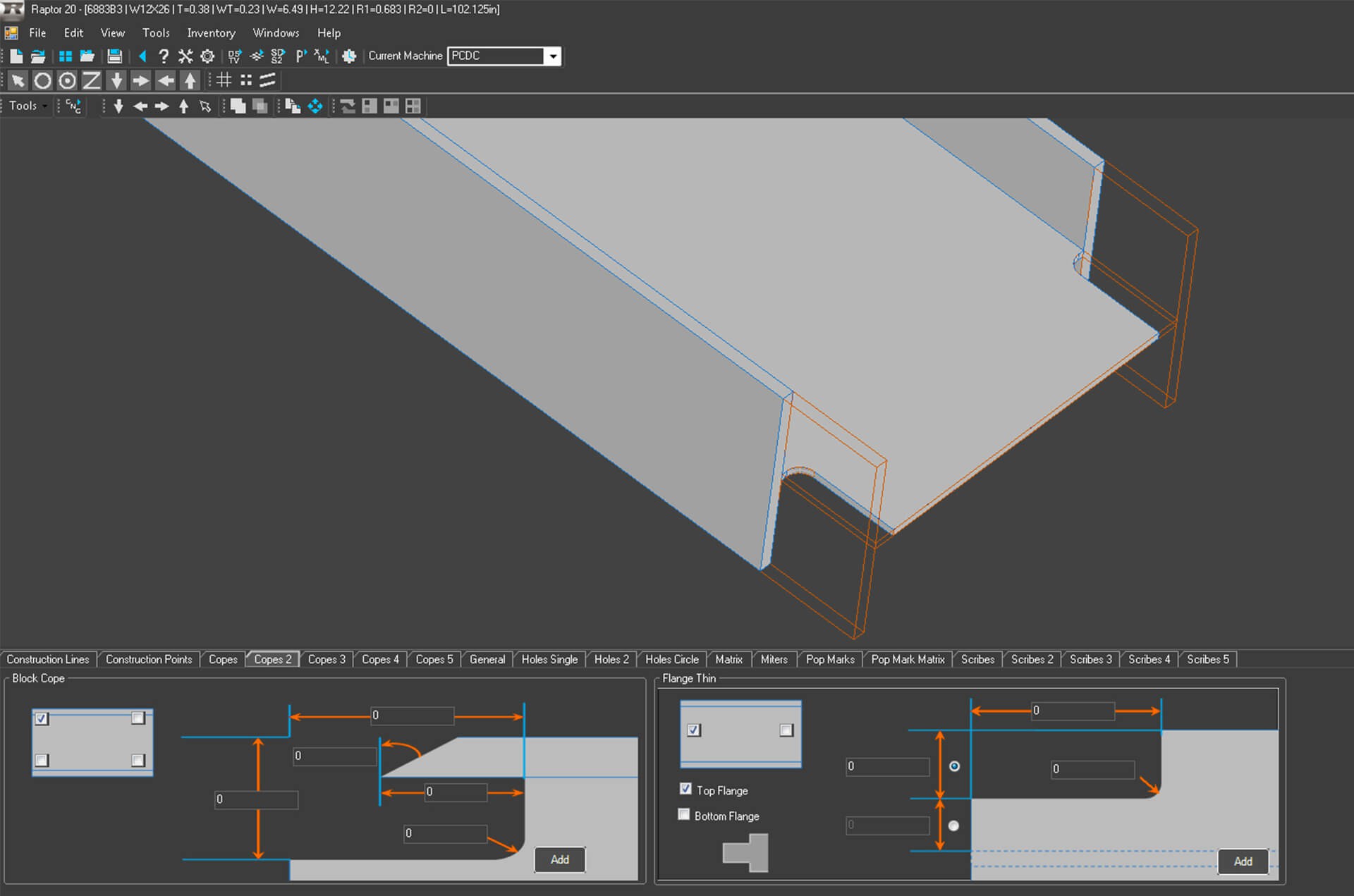
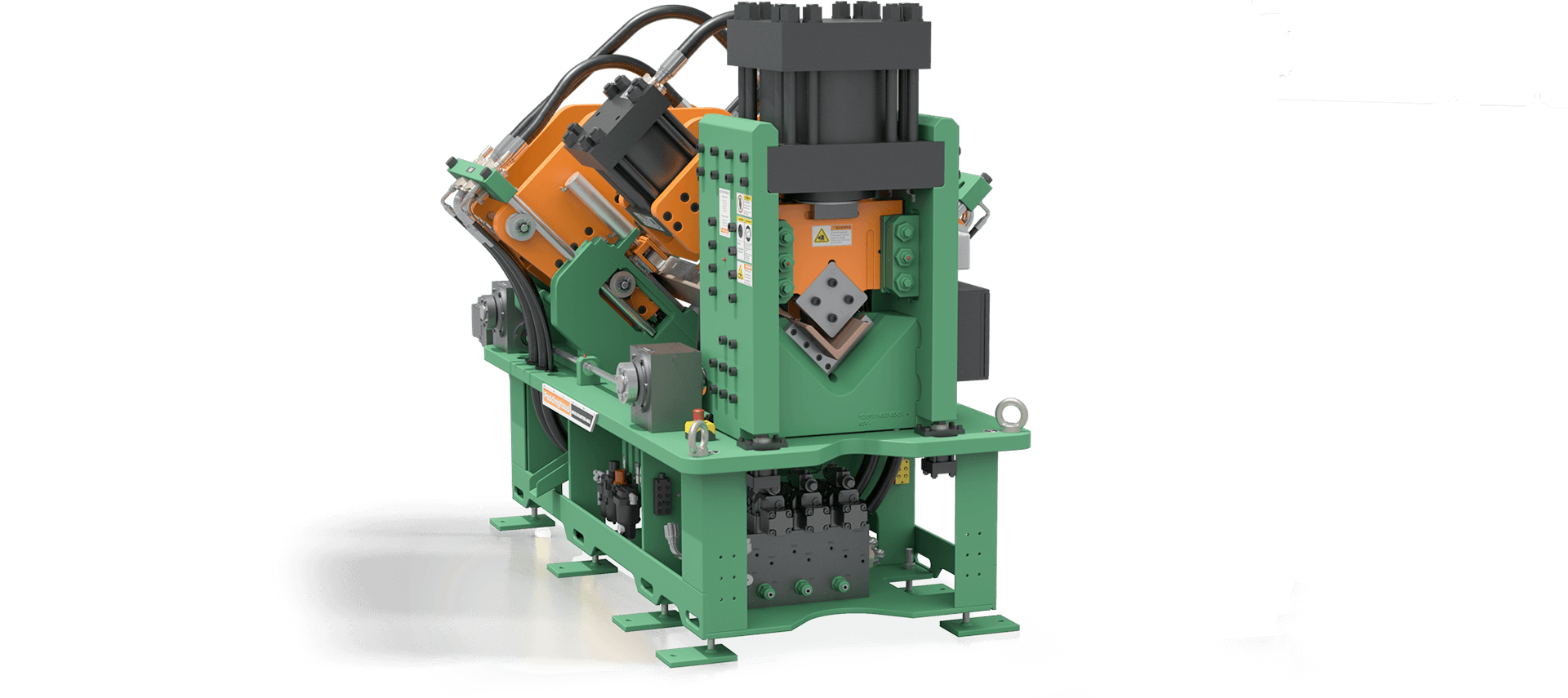
Process Higher Volumes of Angle
Detail components make up the smallest tonnage of any fabricators' workload, but consistently demand the highest amount of labor. Serving as the industry's benchmark for productivity and accuracy, the Anglemaster-663 caters to today's fabricators' need to automate punching, nibbling, shearing and marking for angle and flat bar.
Accurate and Versatile Angle Processing
The Roller Feed drive and measurement system from Peddinghaus has been redesigned to improve accuracy even greater than before. By positioning two encoders on the machine, steel can pass through piece after piece with no stop in production. This innovative patented Roller Feed is designed to flex with the material in order to ensure a constant roll and an accurate measurement given deviations in material, maximizing contact with long parts.
6 Punches for Tooling Capacity
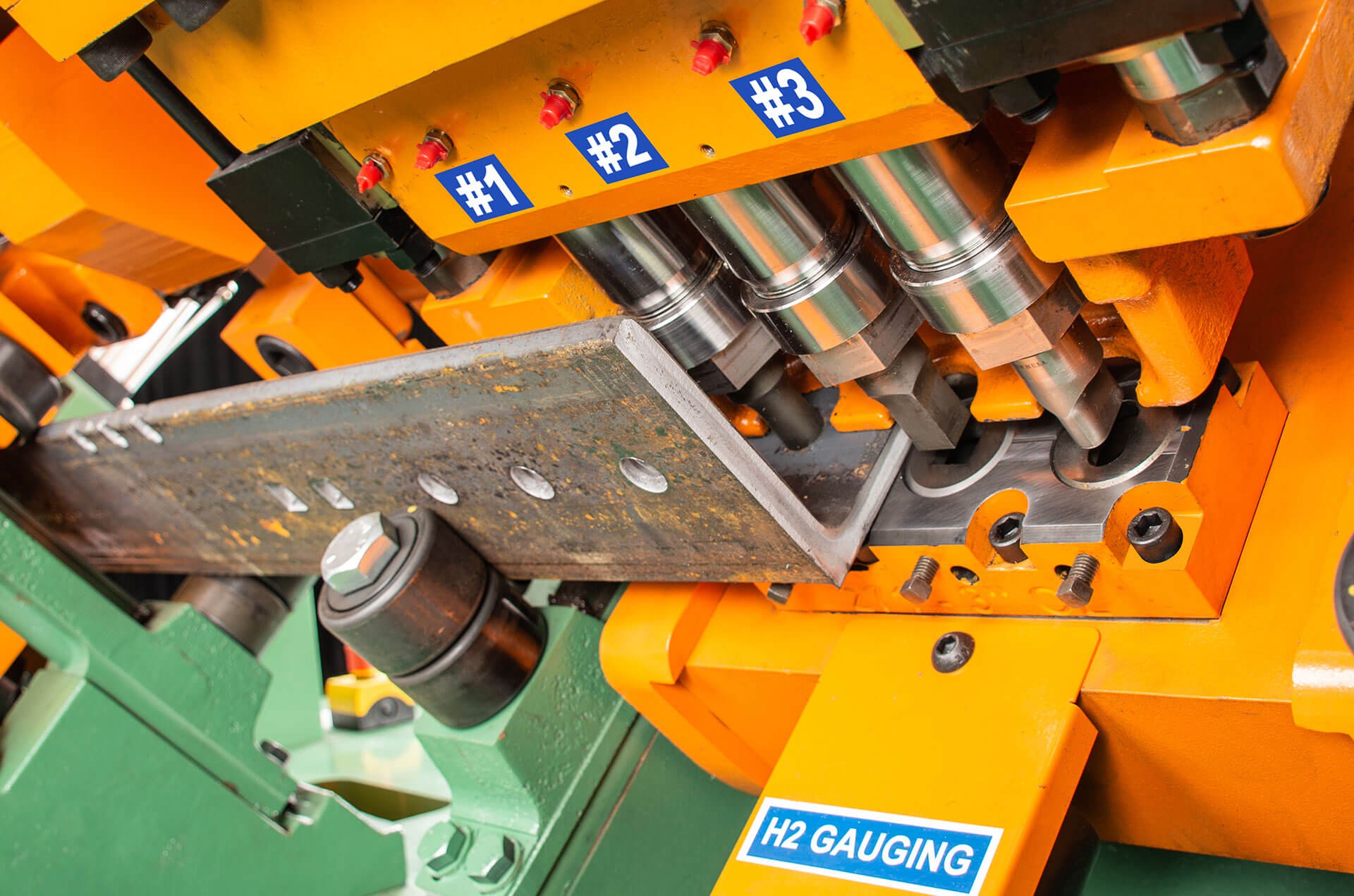
Three punch stations per hydraulic press allow the machine to apply up to three different hole shapes/sizes per leg. A new and improved punch tool design allows for quicker and easier tool changes. This angle line can accommodate shaped holes such as squares, rectangles, obrounds and slots, including a feature that allows nibbling of material for cutting large notches out of angle or flat bar.
Powerful Shearing
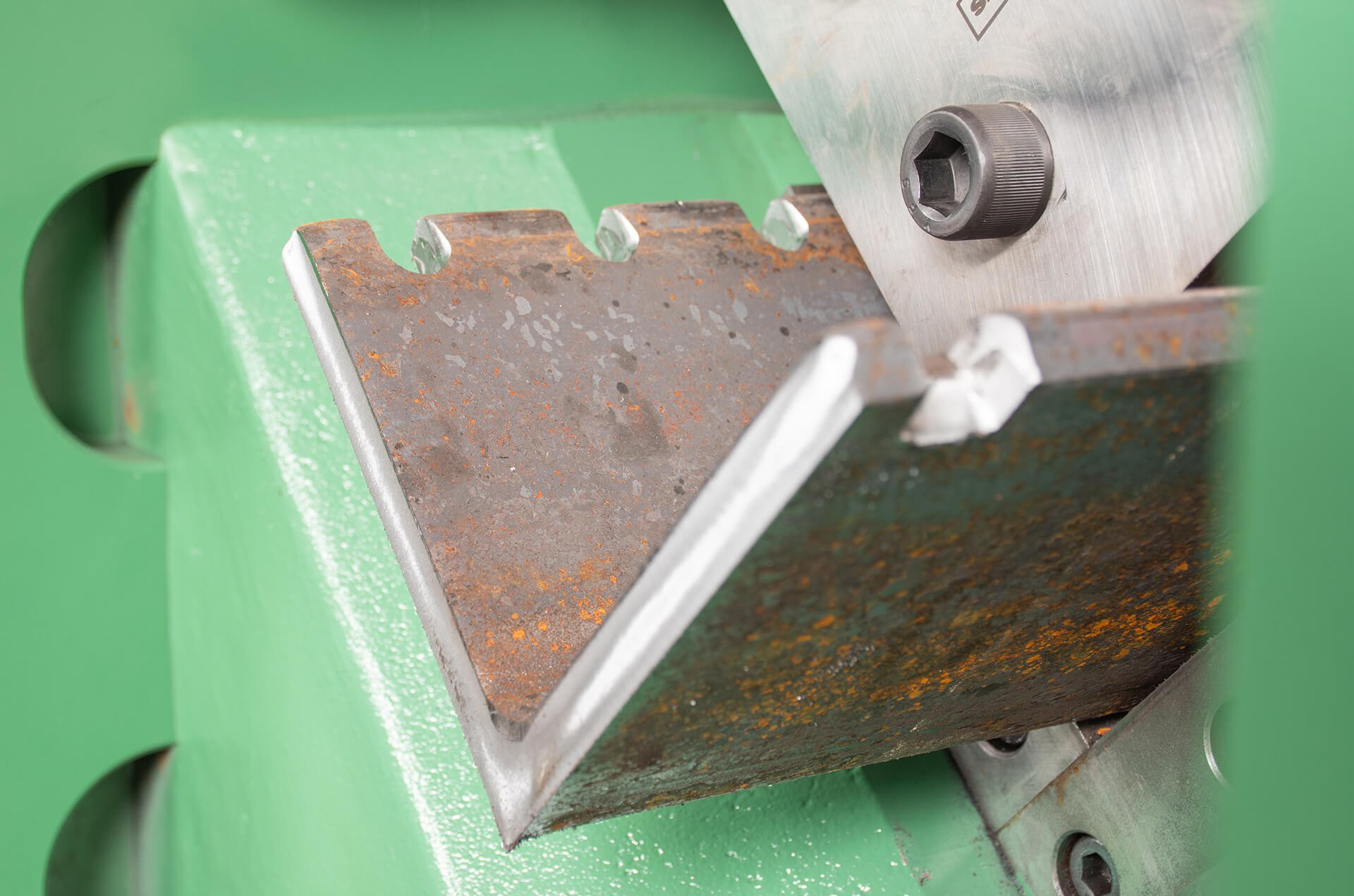
The Anglemaster-663 uses a single cut 320 ton shear press for the cutting to length angle and flat stock. A single cut shear mechanism eliminates the slug created by double cut shear mechanisms.
SignoScript Carbide Scribing
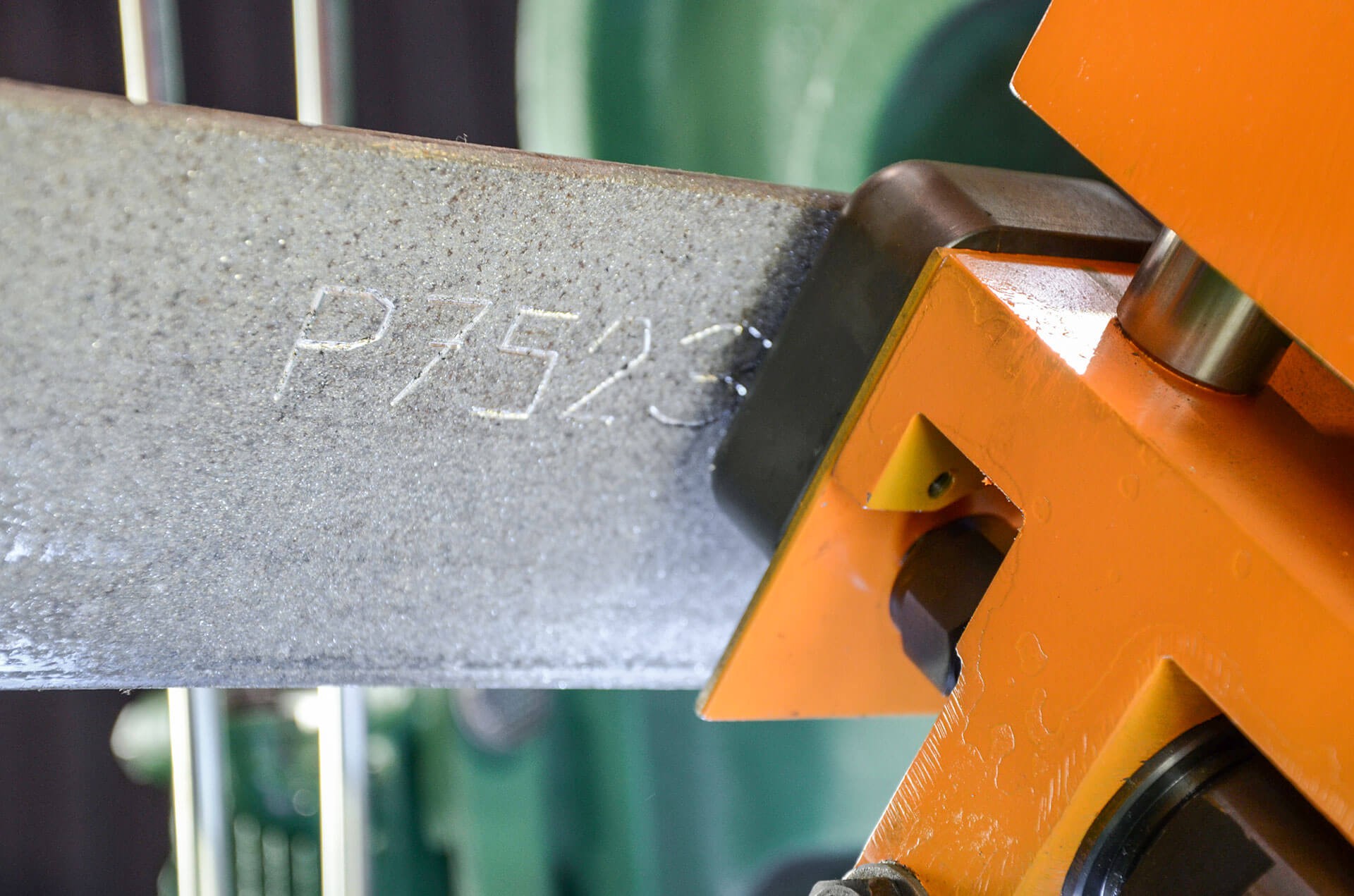
The SignoScript layout marking attachment eliminates human error in manual layout methods. Complete information is maintained throughout blasting, galvanizing and painting processes.
SignoMat Part Stamping
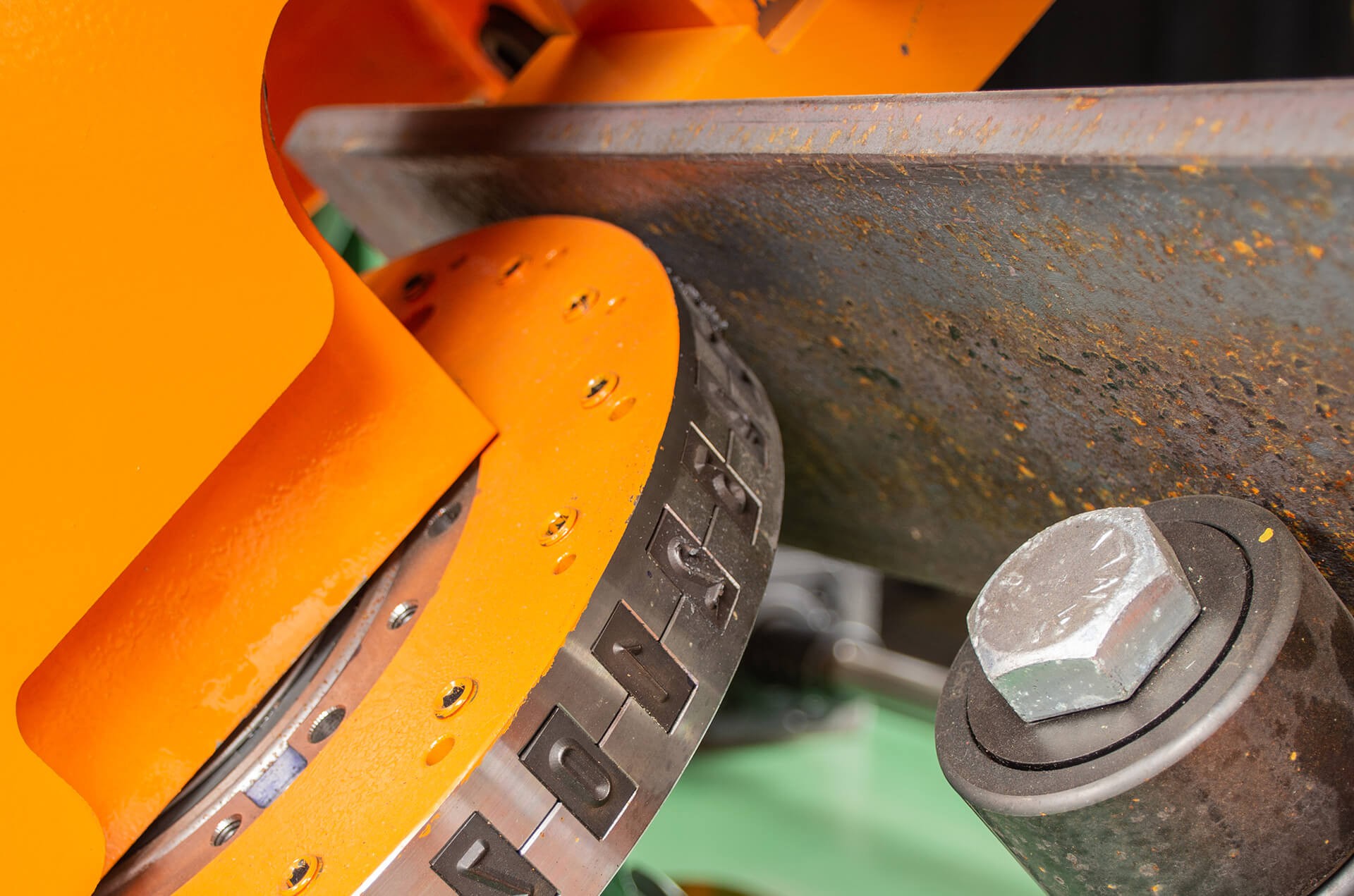
The SignoMat part stamping unit stamps at an unmatched 1 character per second with a depth of 1/32" (.8 mm) and a total height of 1/2" (12 mm). The unit holds up to 36 characters for complete part marking ability.
Nonstop Throughput with Roller Feed Technology
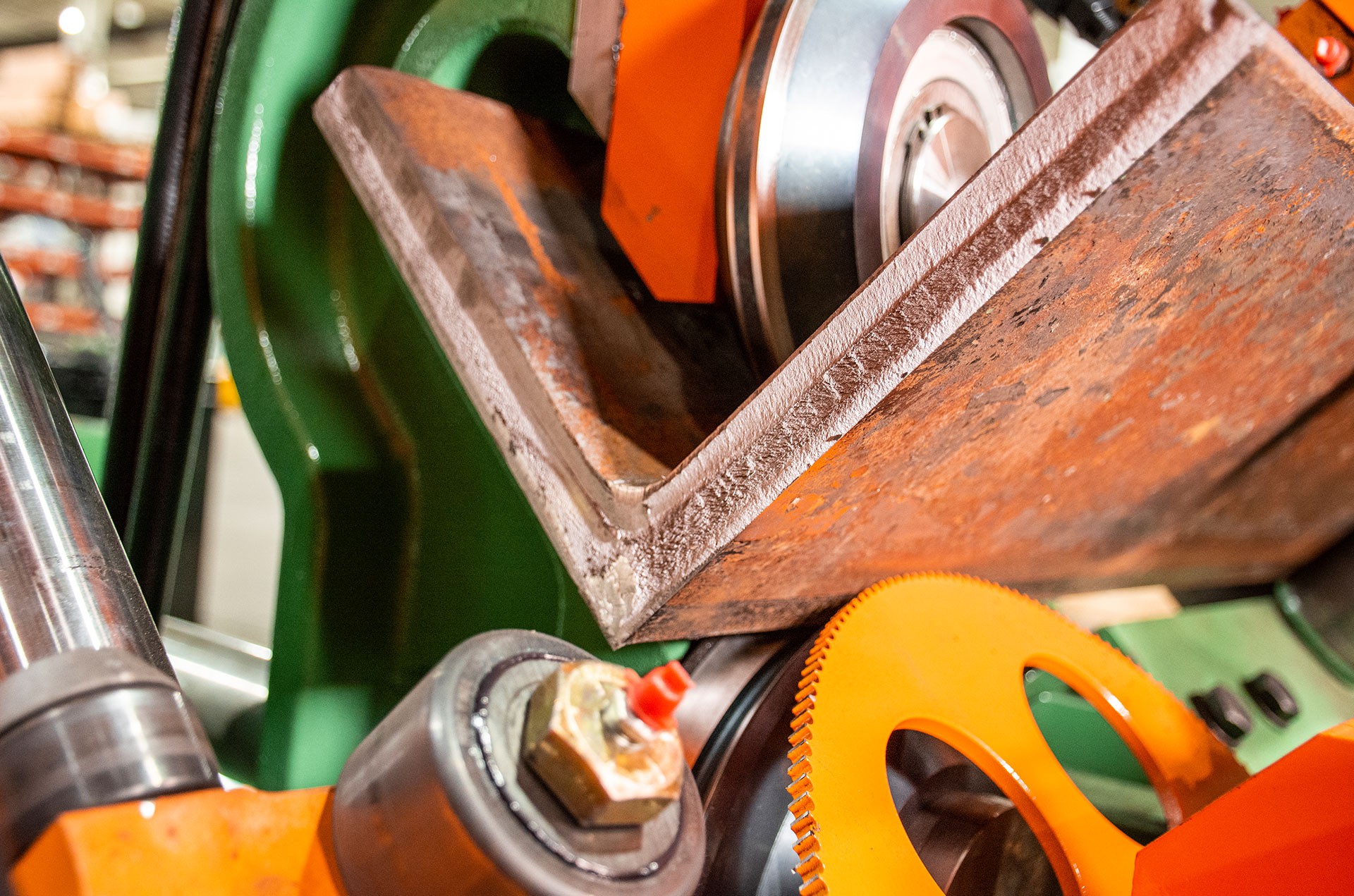
Equipped with the Peddinghaus Roller Feed measurement system, the Anglemaster-663 maximizes contact with the material at all times. This Roller Feed technology ensures a constant roll and an accurate measurement given deviations in material.
Lubrication System Prolongs Tool Life
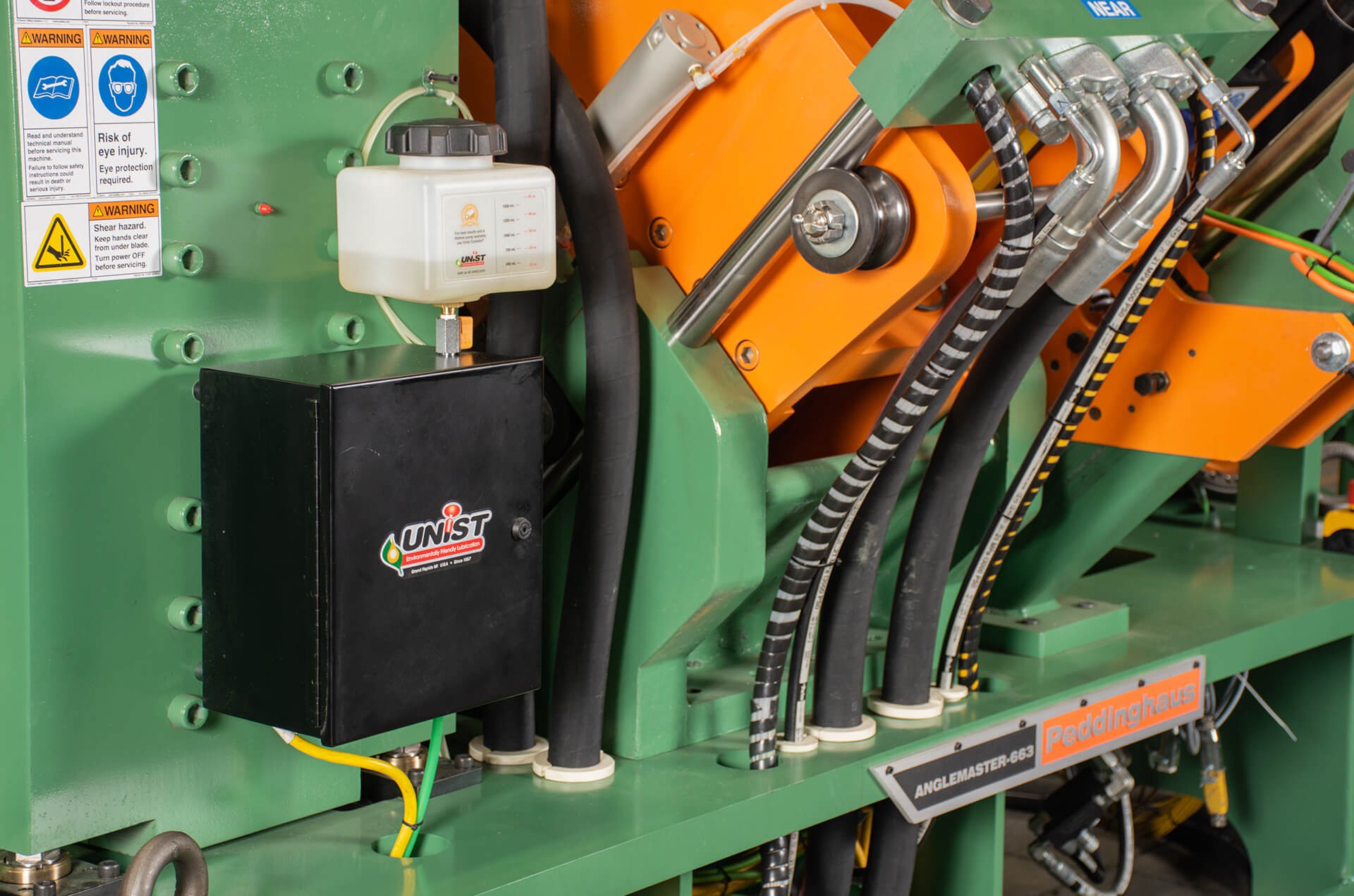
The lubrication system on the Anglemaster-663 angle line extends to the shear, now allowing for longer shear life. Overall angle production and tool life is enhanced with the Minimum Quantity Lubrication (MQL) system.
Infeed and Outfeed Material Handling
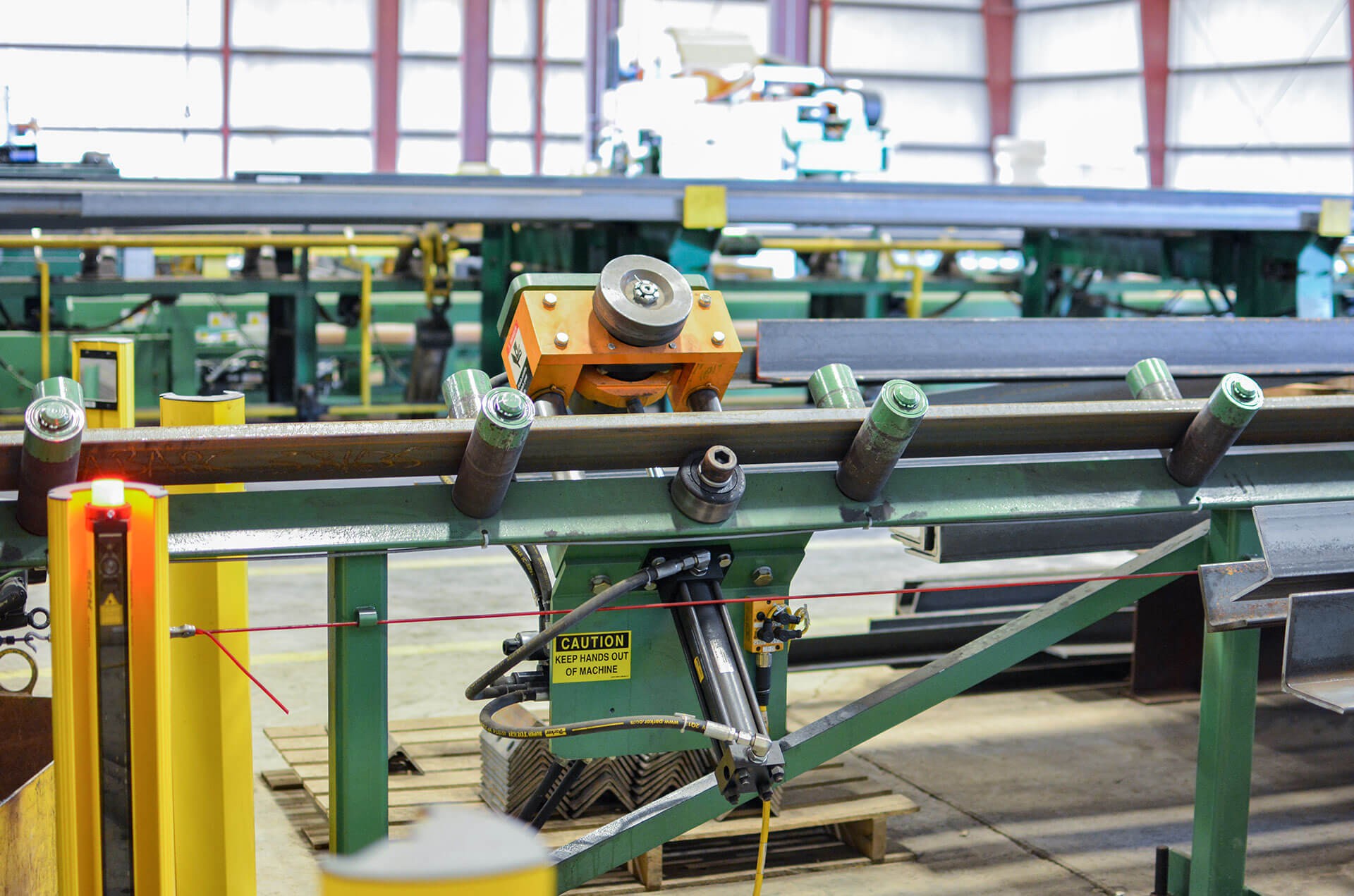
The infeed and outfeed material handling system, designed for continuous production, keeps the operator safe at all times. As drag chain conveyors move material to the infeed conveyors, power material advance initiates steel into the machine. Once sheared, drive rollers advance the finished parts to the unloading zone.