Overview
- Sub-X Beam Drill Line
- High Speed Carbide Drilling
- Slot Milling
- Cope Milling
- Tapping
- Countersinking
- 4-Axis Plasma Marking
- 4-Axis Carbide Scribing
- Three Drill Assemblies
- 6-Station Tool Changers (3)
- Siemens Smart Spindle Motors
- Minimum Quantity Lubrication
- Enhanced Clamping System
- Peddinghaus Control
- Raptor Software
Mill Out
Process
The Impact of Sub-X Processing
A major difference between shops that succeed and shops that fall behind is the investment in new technology. The ability to recognize when the processes you are accustomed to are failing to meet industry standards is paramount to remaining competitive in the structural steel landscape.
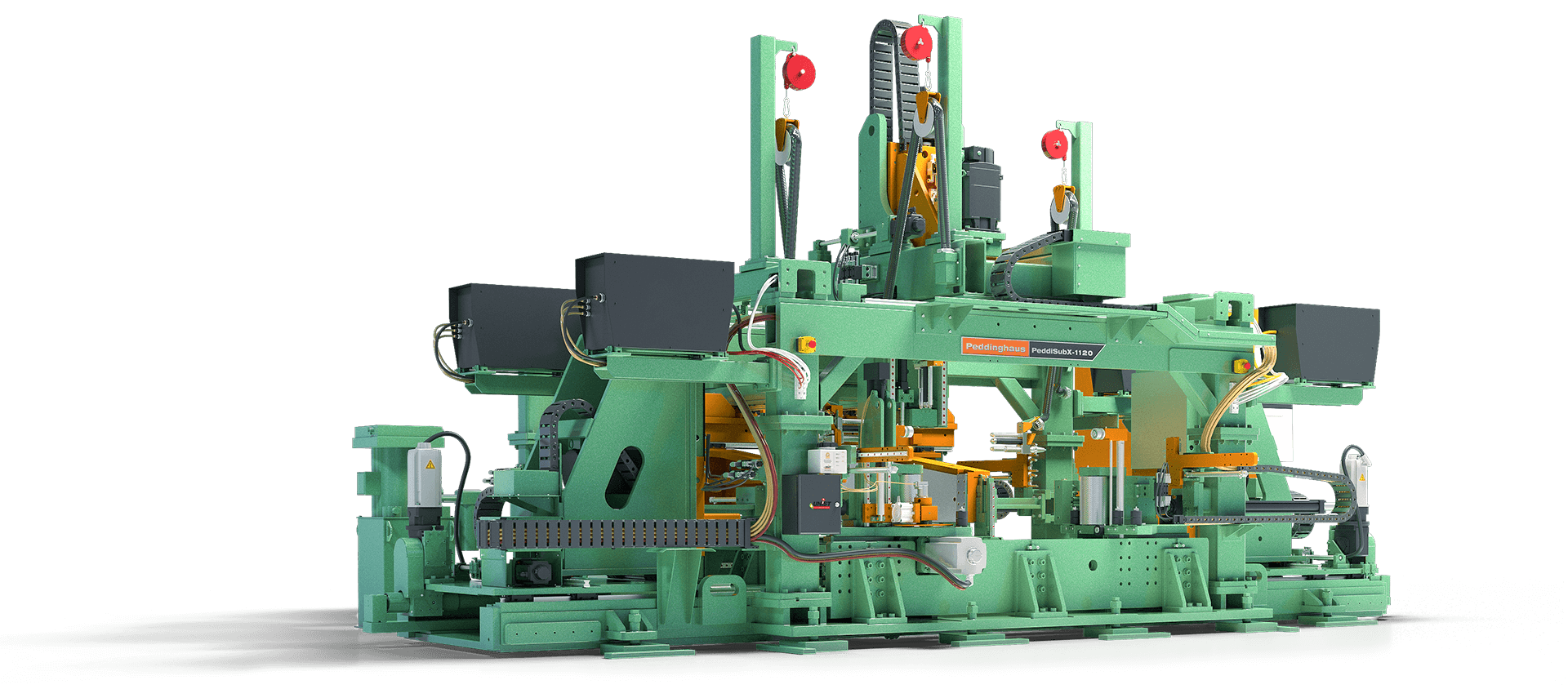
Accelerate Production Timetables
Peddinghaus has rewritten the drilling and milling standard with the PeddiSubX-1120 beam drill line. By rapidly decreasing the time it takes to process profiles, we have given the steel fabrication industry a way to keep production timetables ahead of schedule for years to come.
High Speed Carbide Drilling and Milling
Speedy 25 HP Sub-X spindles on the PeddiSubX-1120 are each equipped with 6-station tool changers. With the ability to mill out copes in just 90 seconds, the PeddiSubX-1120 has revolutionized structural steel drilling technology once again. An operating area of 19-11/16” (500 mm) per spindle allows processing on an entire section of material without spindle downtime.
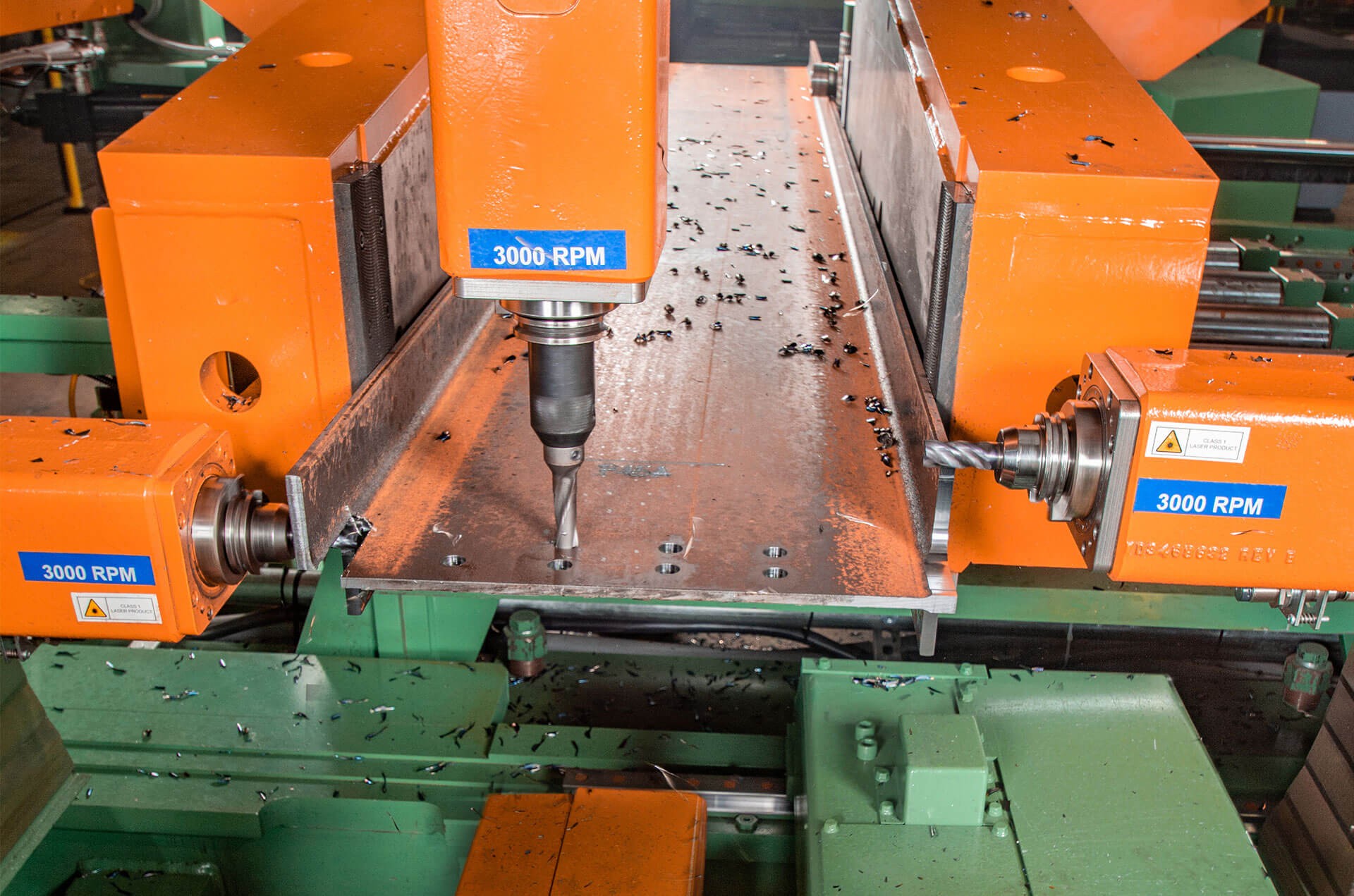
Plasma Marking and Clear Carbide Scribing
Mark on all four sides of material simultaneously with plasma marking and carbide scribing. Optional part marking tools are stored within each of the drilling axes and selected upon program command.
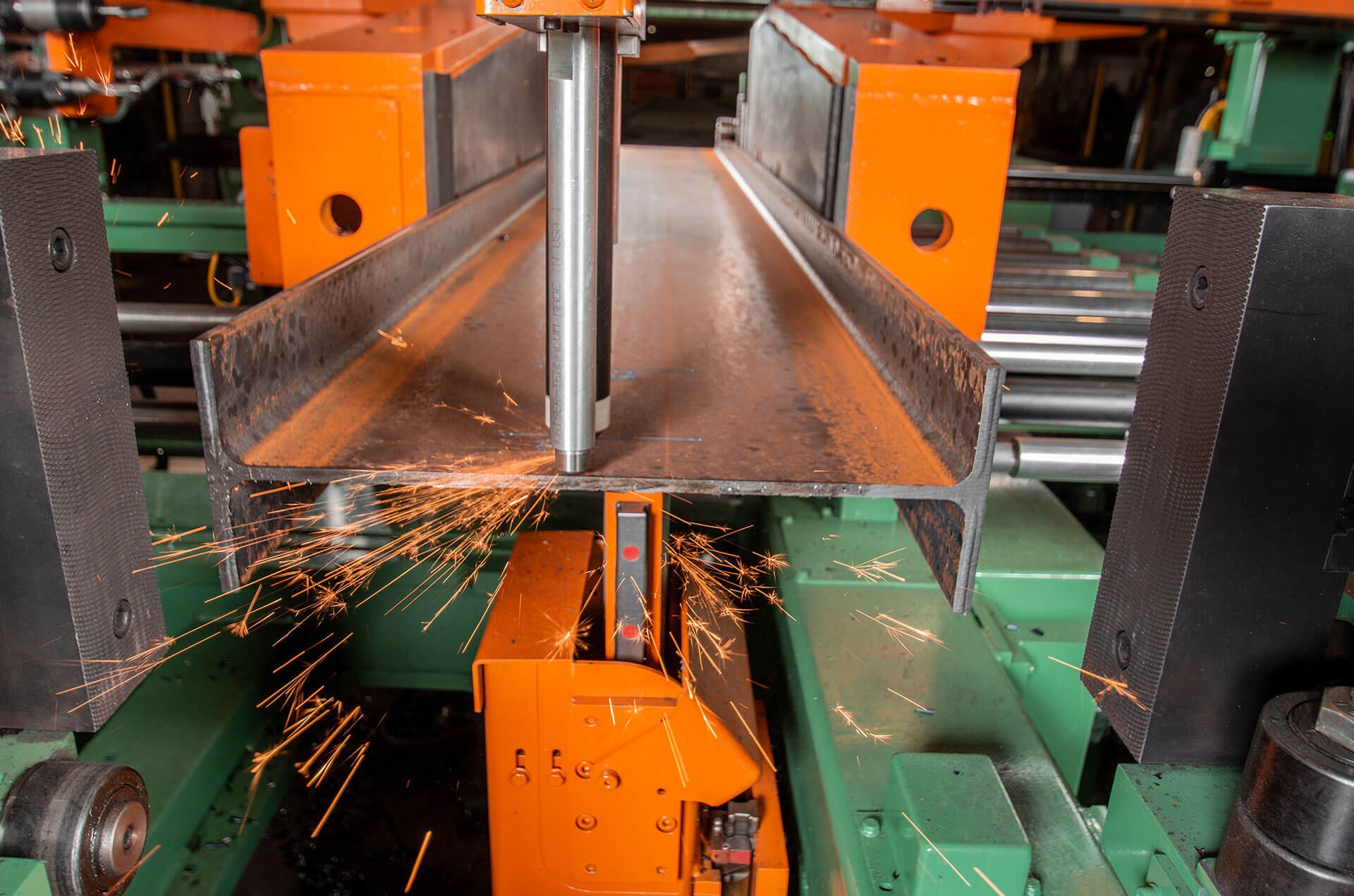
Nonstop Throughput with Roller Feed Measurement
Peddinghaus’ Roller Feed Measurement system exceeds the industry standard for roller measurement technology. Maintaining accurate measurements without any hesitation in production is crucial. Accuracy is not compromised even despite deviations in material.
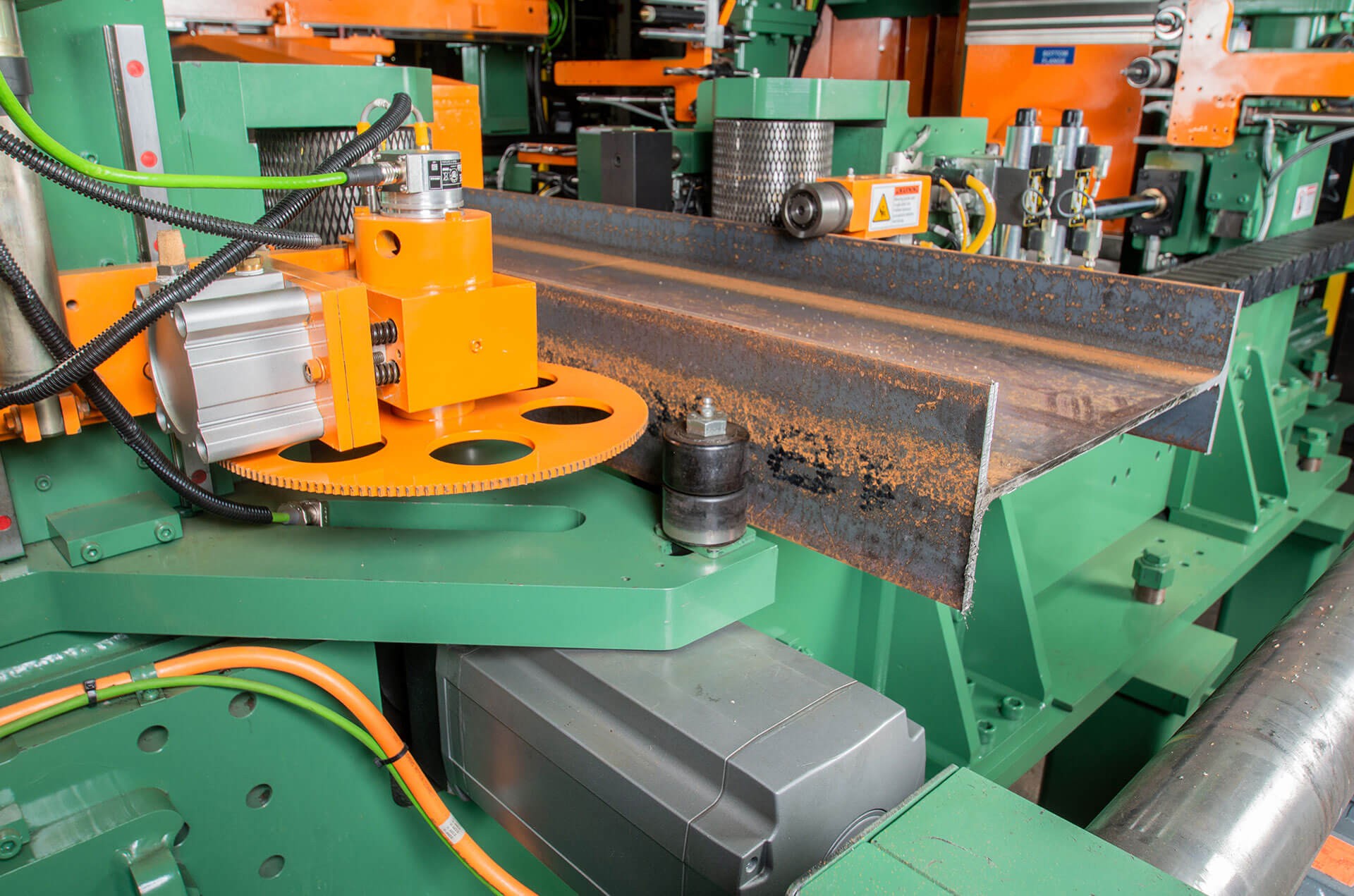
Enhanced Clamping System to Eliminate Vibration
The PeddiSubX-1120 beam drill line employs the most aggressive 14-point clamping system for maximum rigidity of the workpiece. Carbide drilling, milling and tool life is best achieved with the least amount of vibration possible.
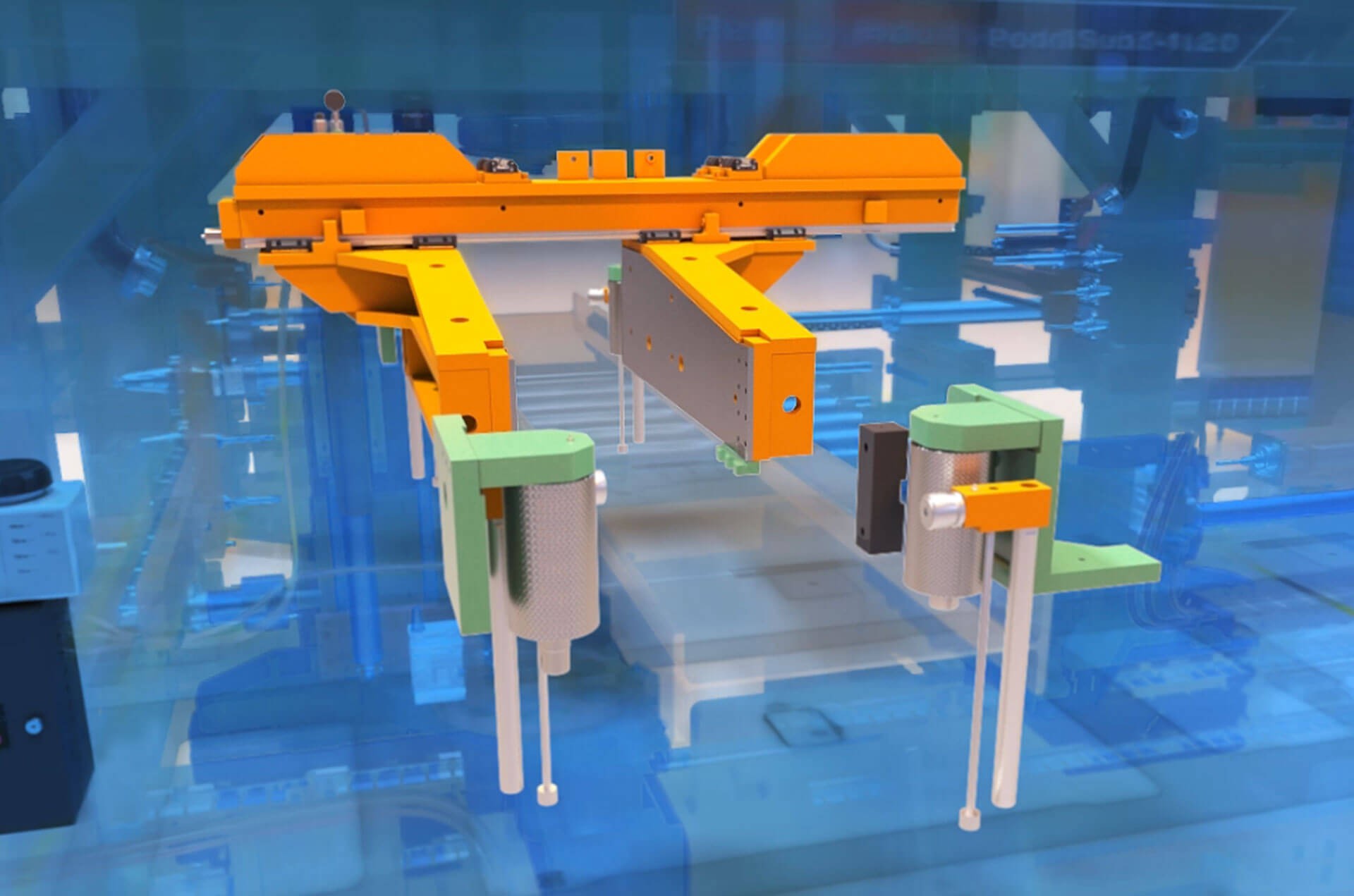
Band Saw Integration
The PeddiSubX-1120’s drilling, milling and marking processes are ideal for tandem installations with any of Peddinghaus' automatic sawing systems.
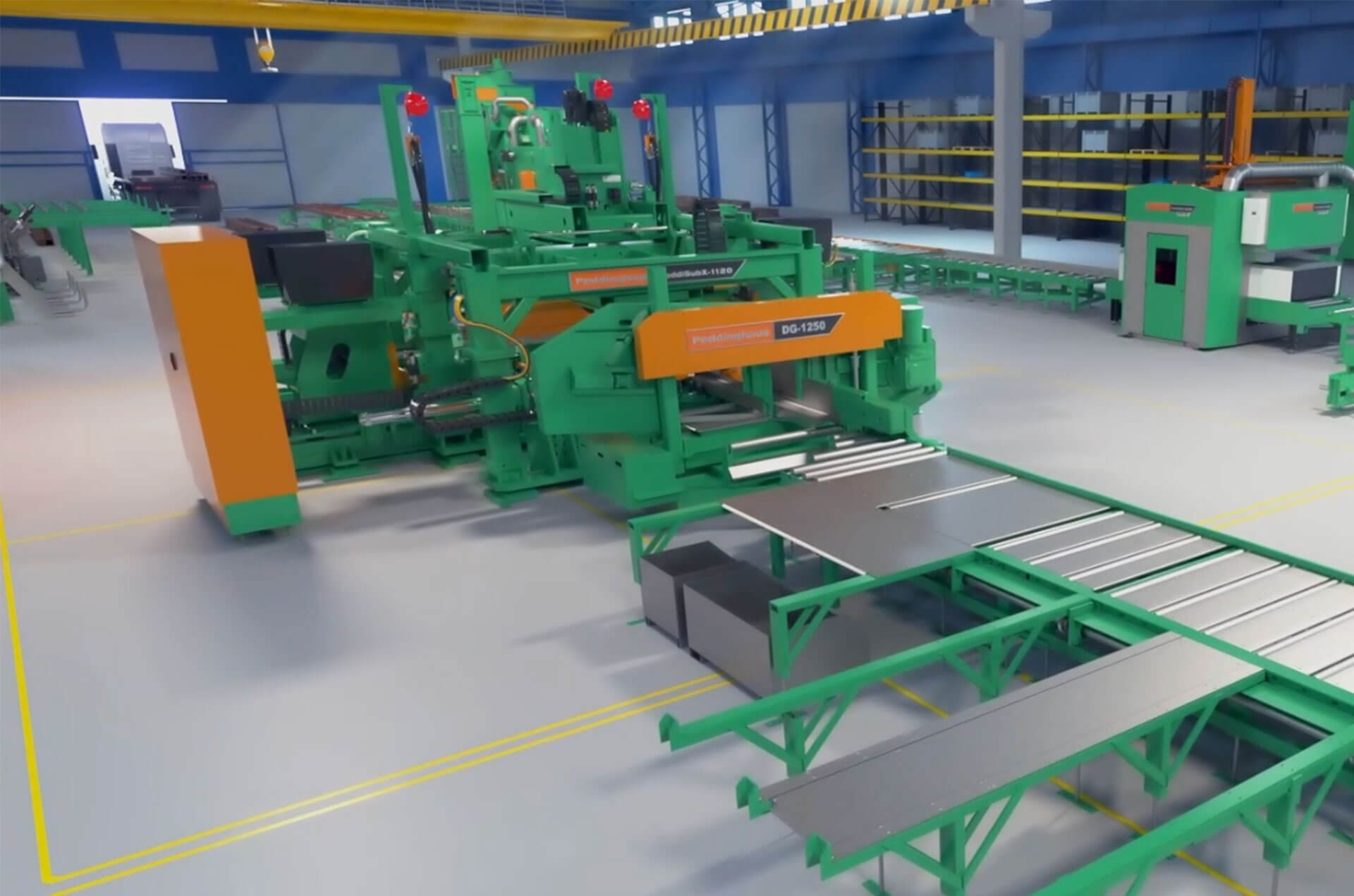
MultMaster Measurement System For Remnants
The MultMaster works as an extension of the Roller Feed measurement system in order to perform cuts which may otherwise require manual positioning for programs with many small pieces. This accessory allows fast and simple material processing on a Peddinghaus drill and saw tandem system by automating the processing of short remnant sections.
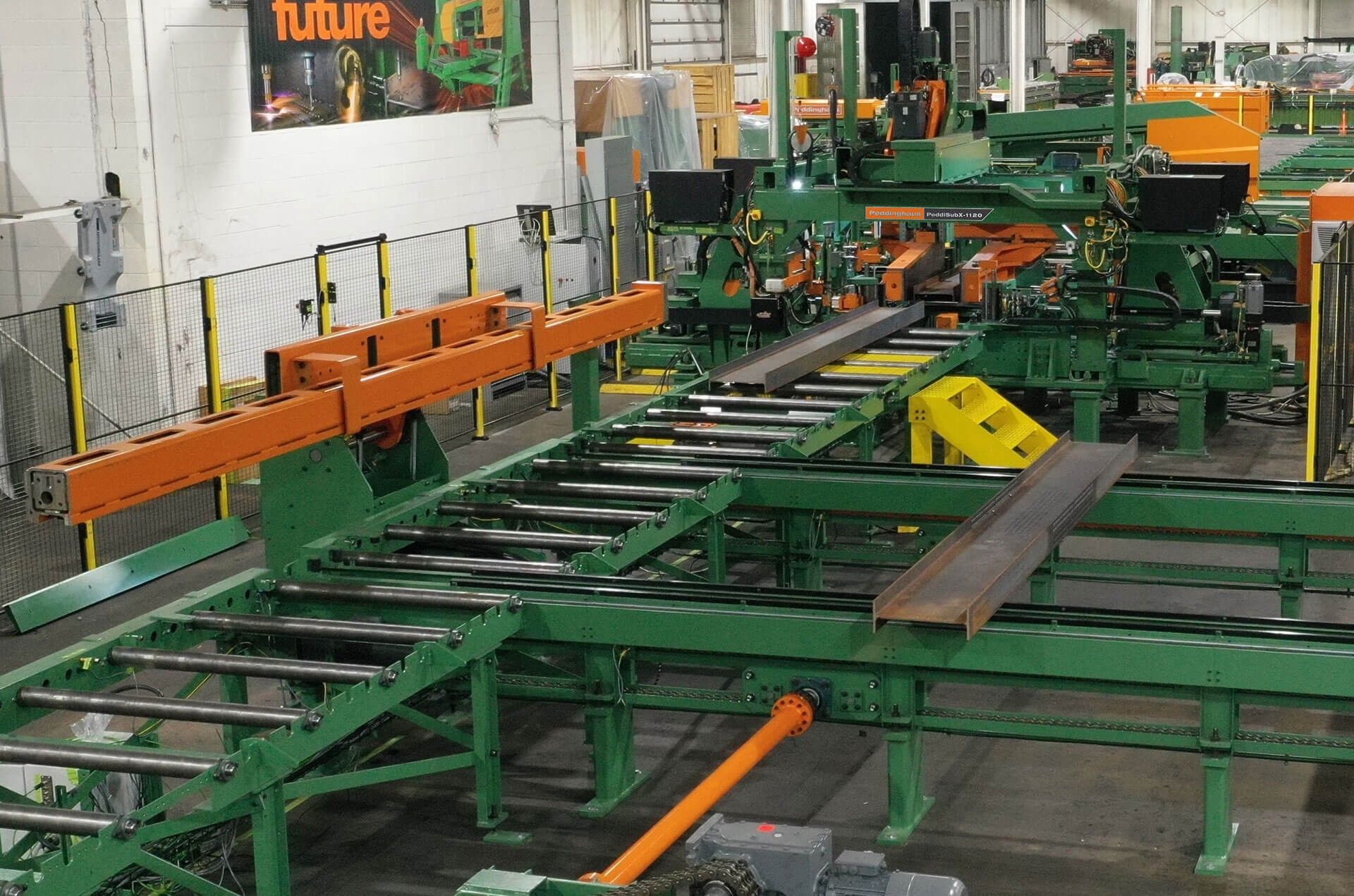
Raptor 3D CAD/CAM Software
Developed by Peddinghaus, Raptor 3D CAD/CAM Software takes CNC innovation further by enabling users to program faster and more accurately. Inspect, modify and export part information directly within the 3D platform. This coupled with Peddinghaus CNC technology means maximum capacity for fabricators.
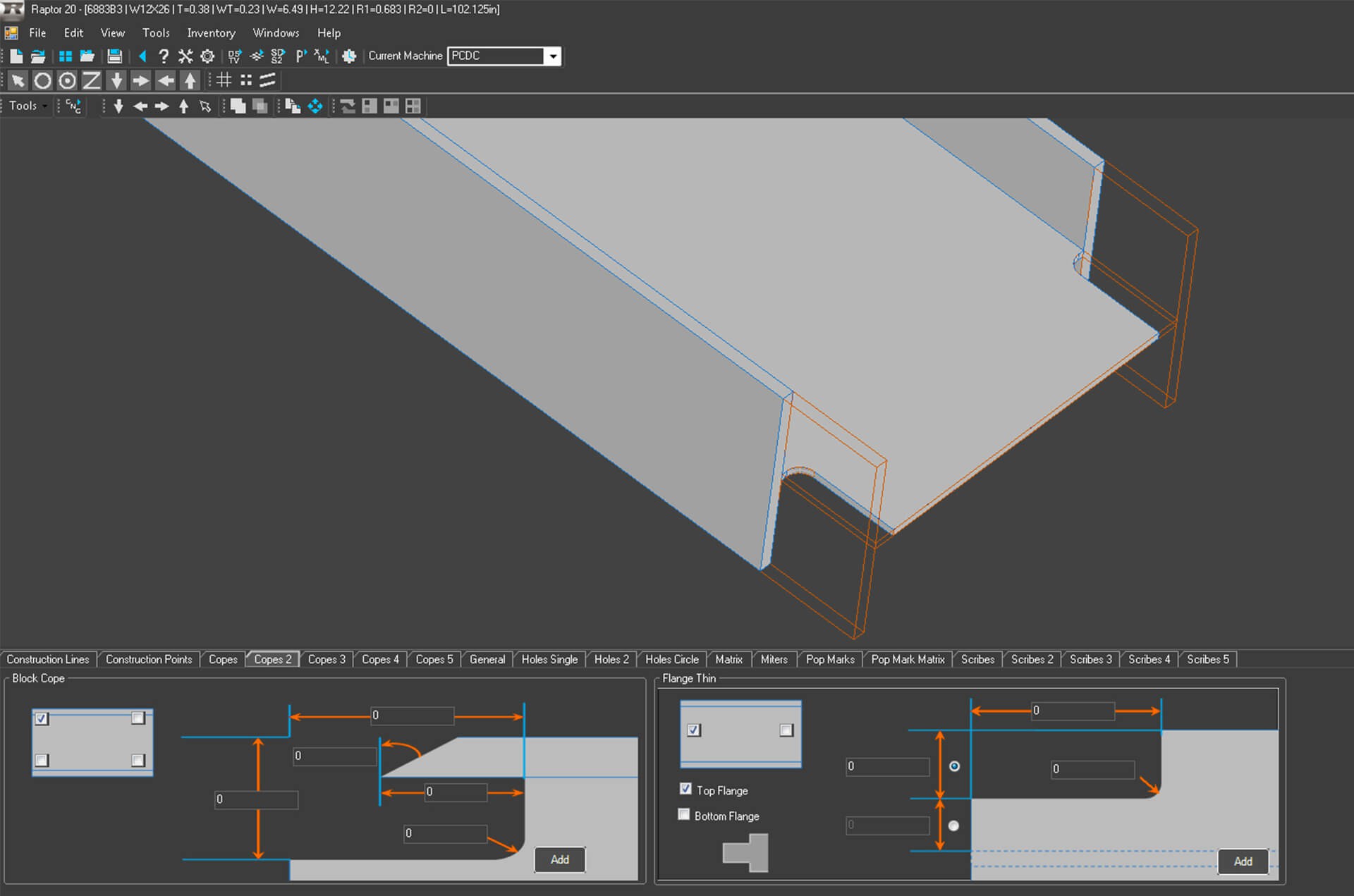
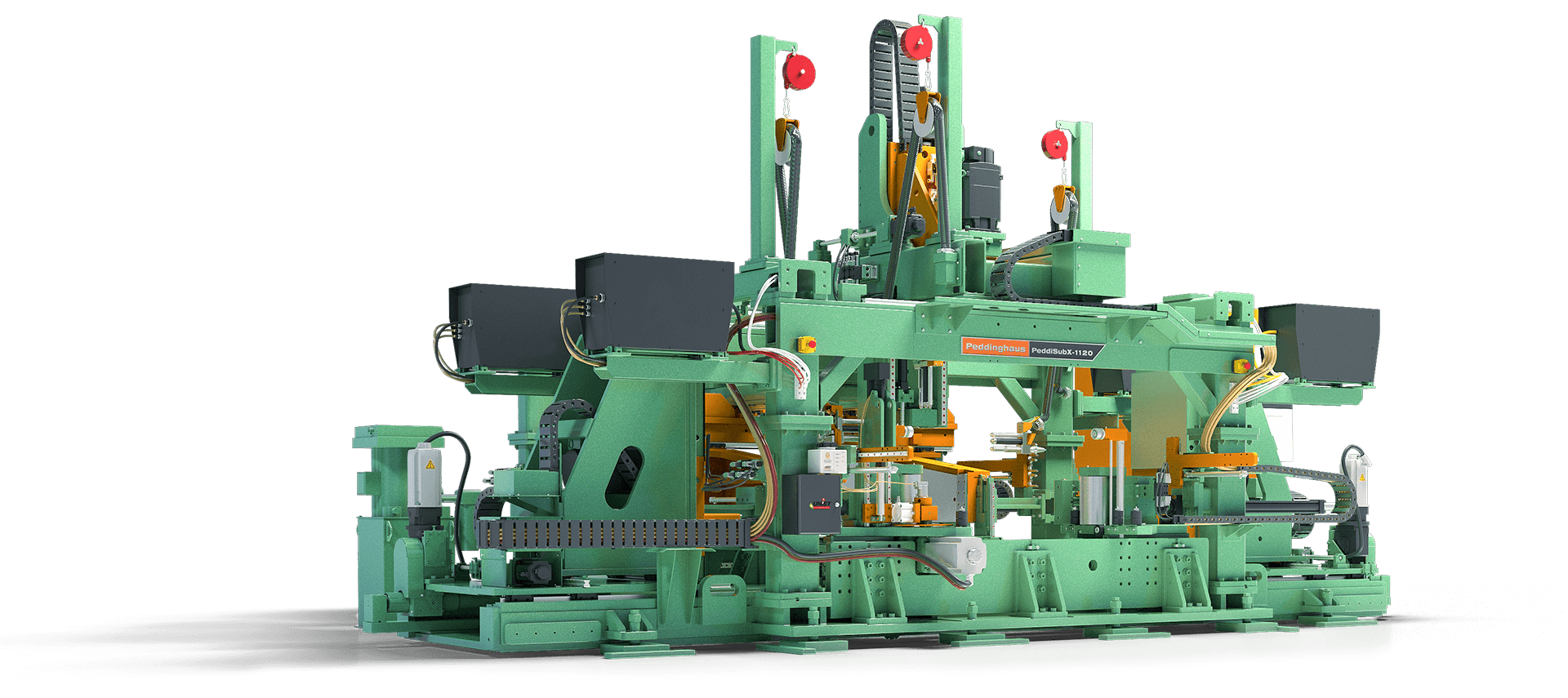
The Impact of Sub-X Processing
A major difference between shops that succeed and shops that fall behind is the investment in new technology. The ability to recognize when the processes you are accustomed to are failing to meet industry standards is paramount to remaining competitive in the structural steel landscape.
Accelerate Production Timetables
Peddinghaus has rewritten the drilling and milling standard with the PeddiSubX-1120 beam drill line. By rapidly decreasing the time it takes to process profiles, we have given the steel fabrication industry a way to keep production timetables ahead of schedule for years to come.
High Speed Carbide Drilling and Milling
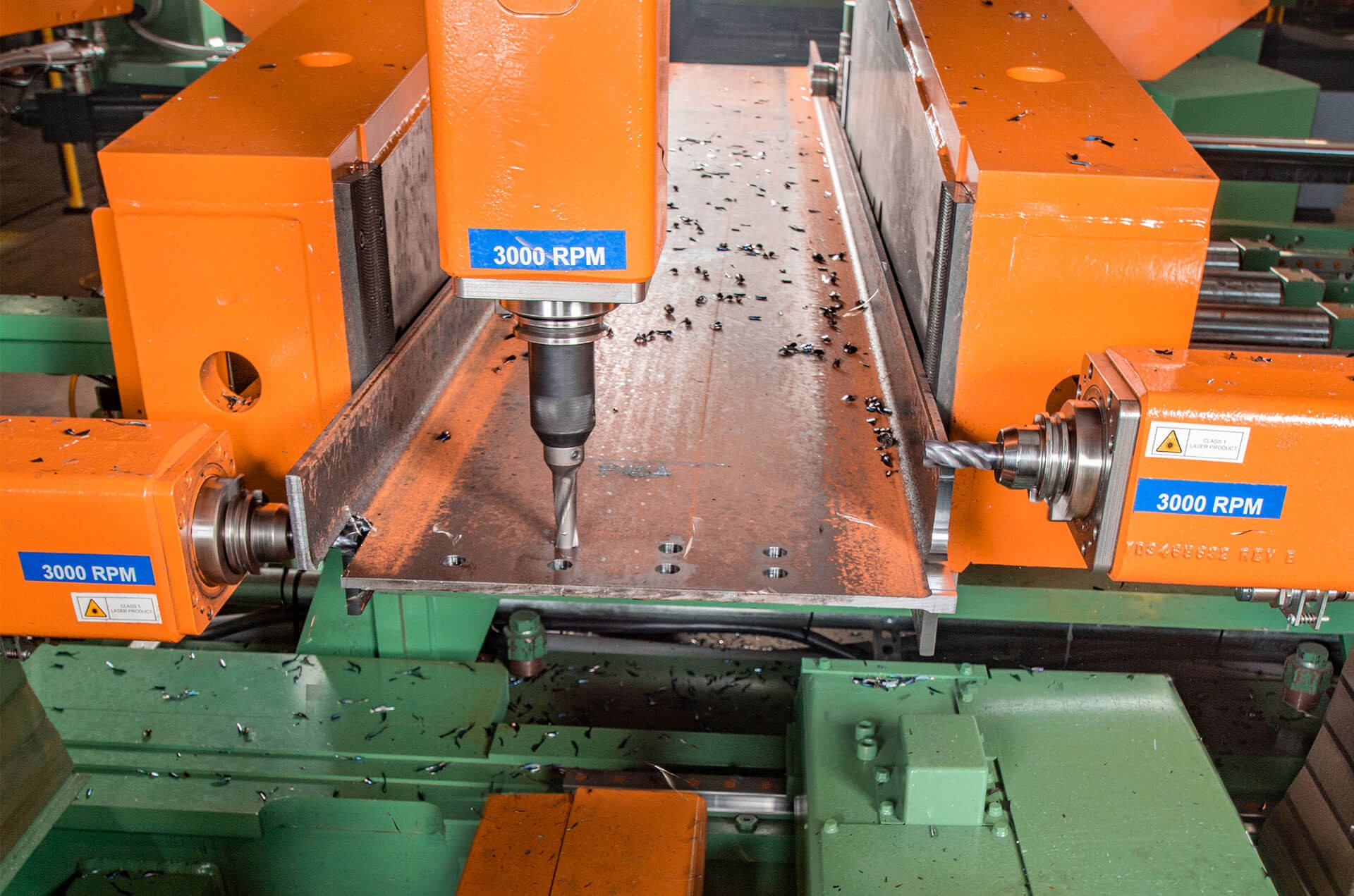
Speedy 25 HP Sub-X spindles on the PeddiSubX-1120 are each equipped with 6-station tool changers. With the ability to mill out copes in just 90 seconds, the PeddiSubX-1120 has revolutionized structural steel drilling technology once again. An operating area of 19-11/16” (500 mm) per spindle allows processing on an entire section of material without spindle downtime.
Plasma Marking and Clear Carbide Scribing
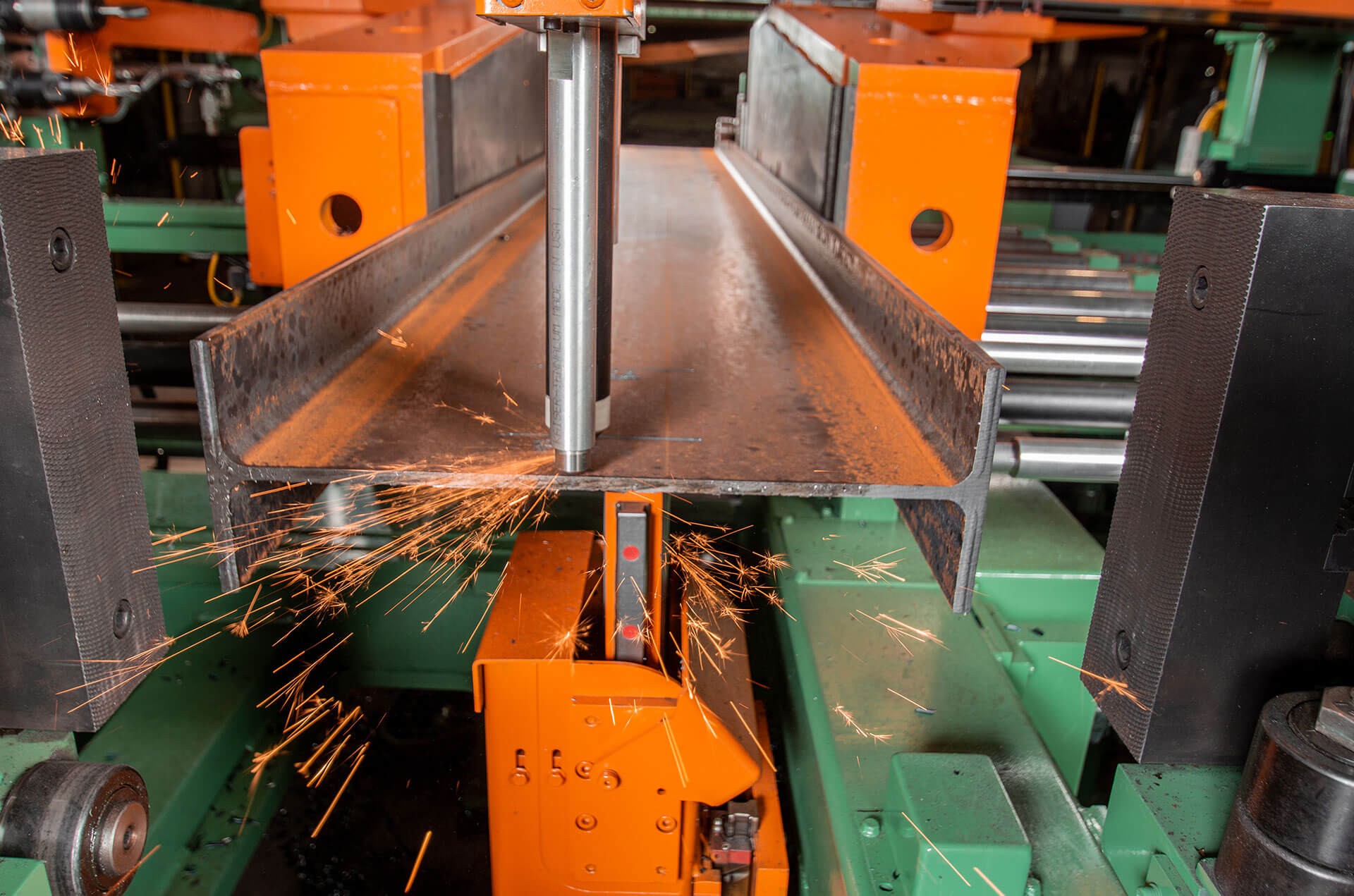
Mark on all four sides of material simultaneously with plasma marking and carbide scribing. Optional part marking tools are stored within each of the drilling axes and selected upon program command.
Nonstop Throughput with Roller Feed Measurement
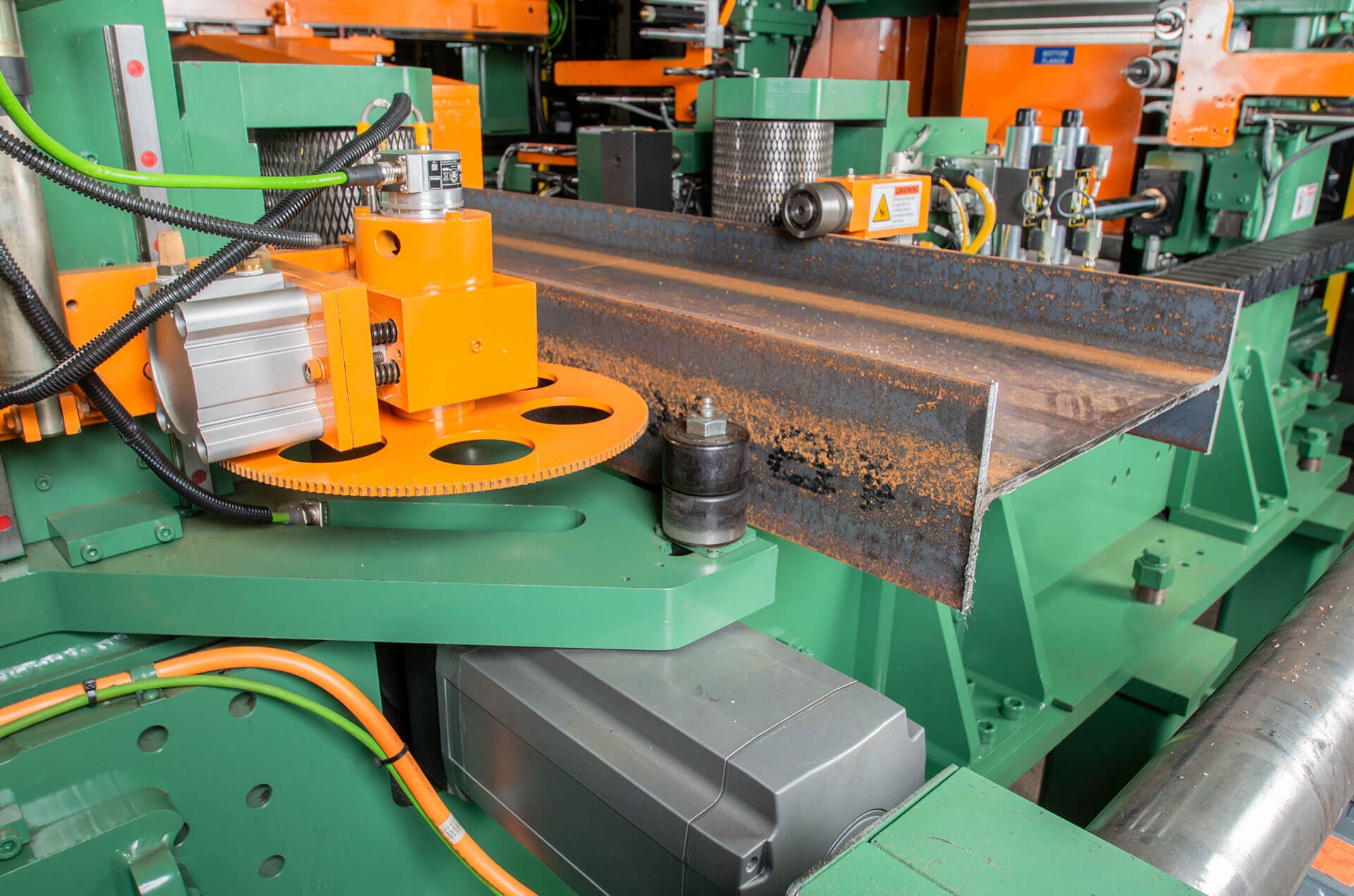
Peddinghaus’ Roller Feed Measurement system exceeds the industry standard for roller measurement technology. Maintaining accurate measurements without any hesitation in production is crucial. Accuracy is not compromised even despite deviations in material.
Enhanced Clamping System to Eliminate Vibration
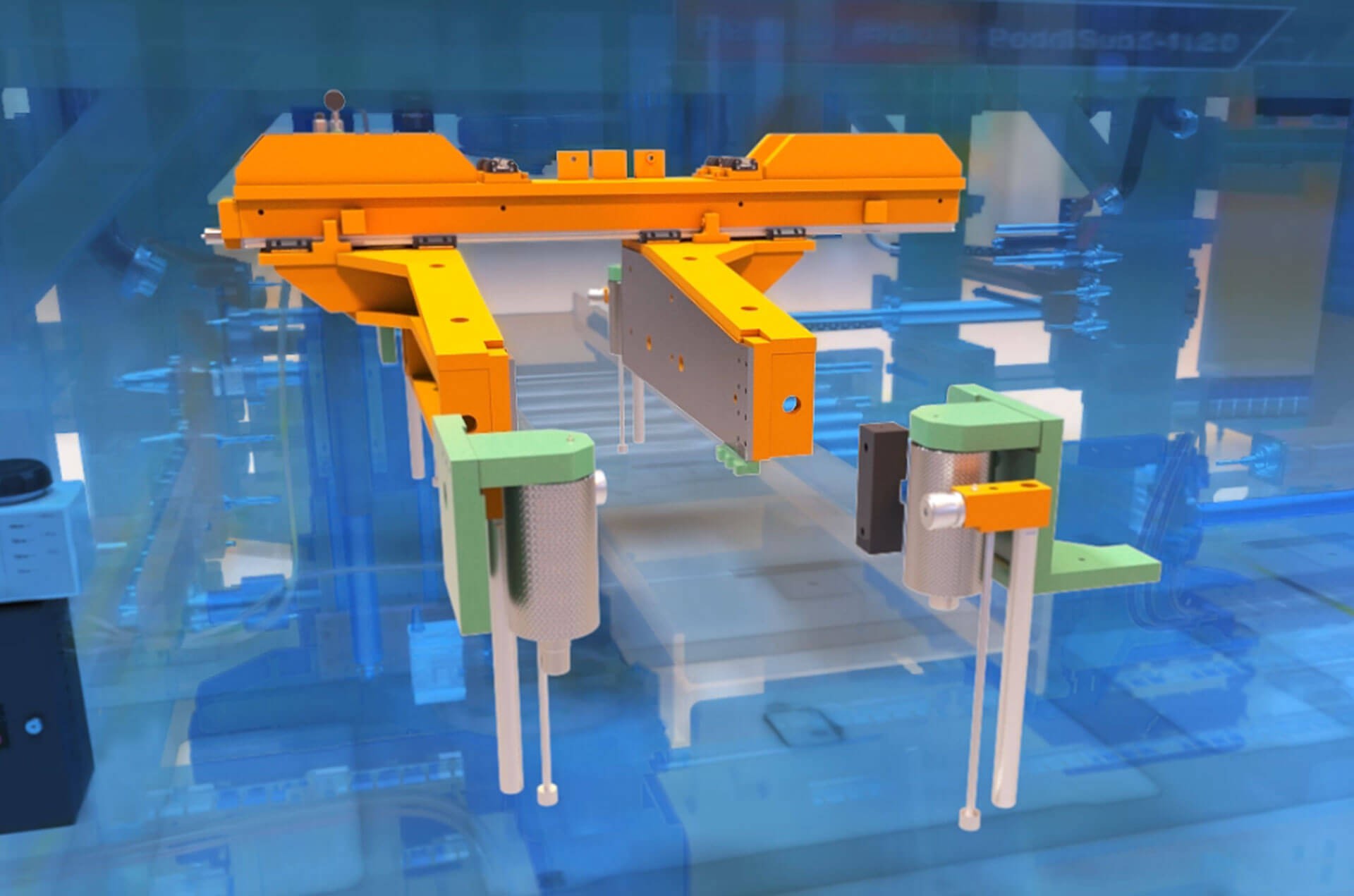
The PeddiSubX-1120 beam drill line employs the most aggressive 14-point clamping system for maximum rigidity of the workpiece. Carbide drilling, milling and tool life is best achieved with the least amount of vibration possible.
Band Saw Integration
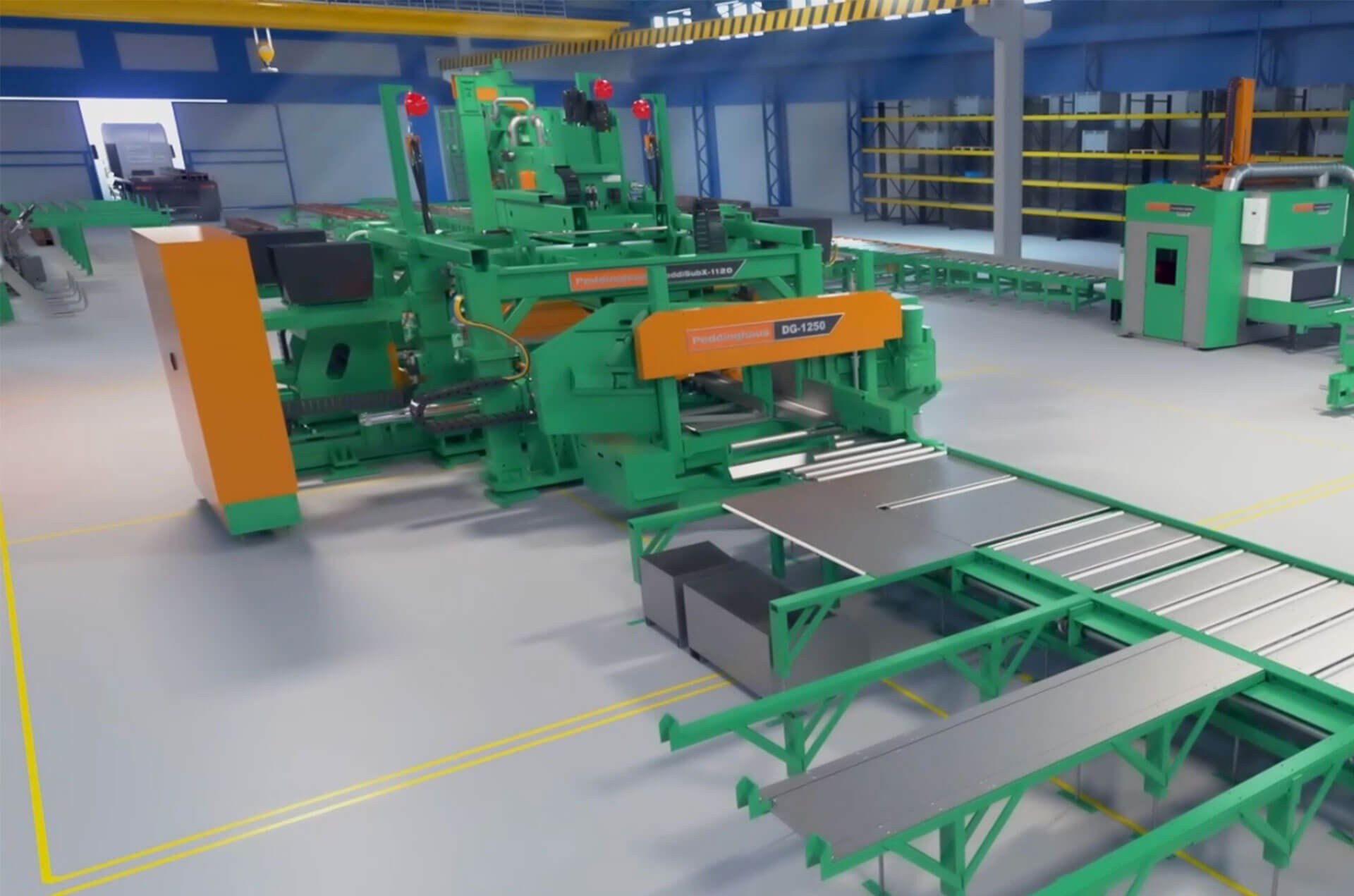
The PeddiSubX-1120’s drilling, milling and marking processes are ideal for tandem installations with any of Peddinghaus' automatic sawing systems.
MultMaster Measurement System For Remnants
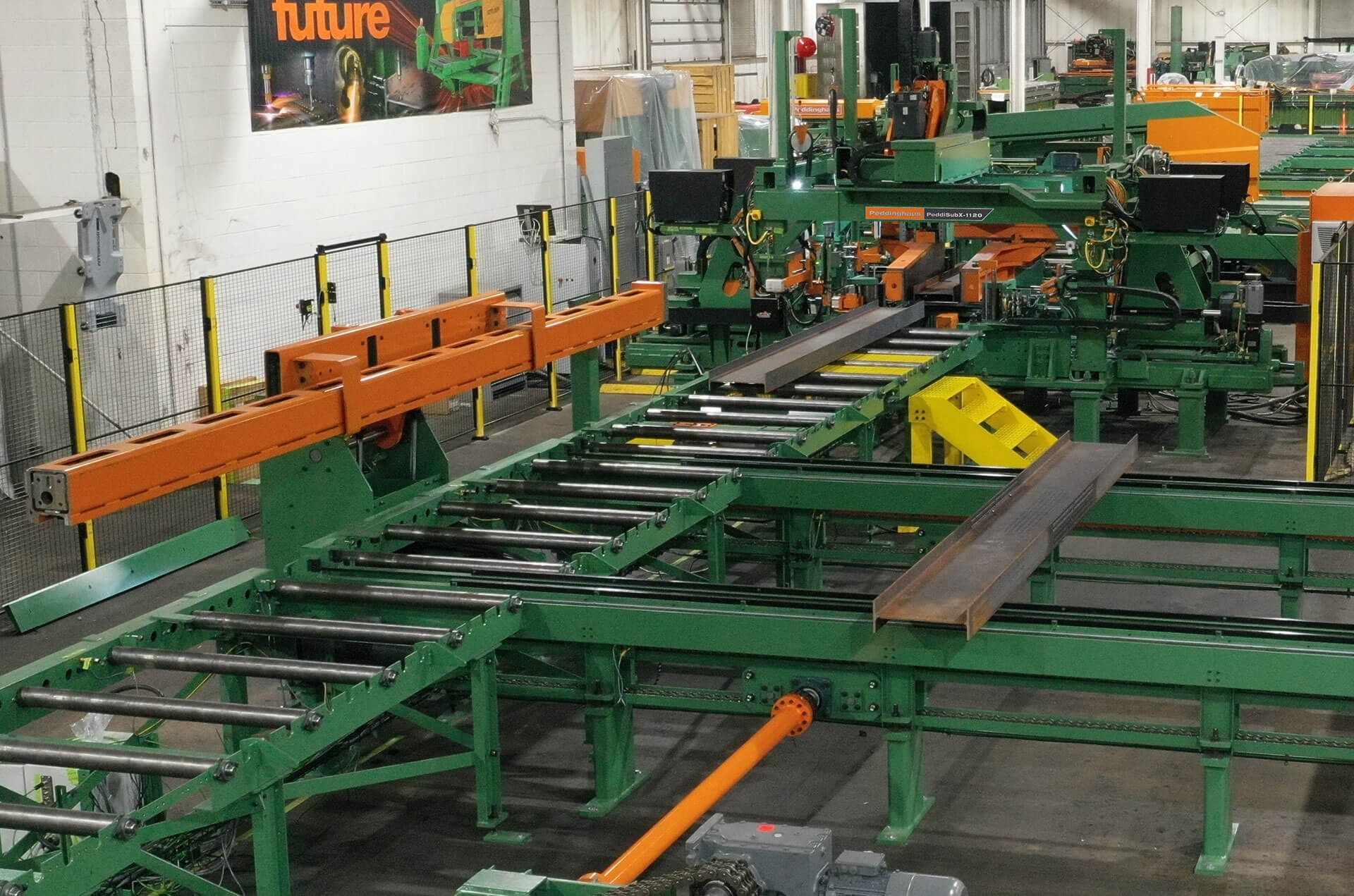
The MultMaster works as an extension of the Roller Feed measurement system in order to perform cuts which may otherwise require manual positioning for programs with many small pieces. This accessory allows fast and simple material processing on a Peddinghaus drill and saw tandem system by automating the processing of short remnant sections.